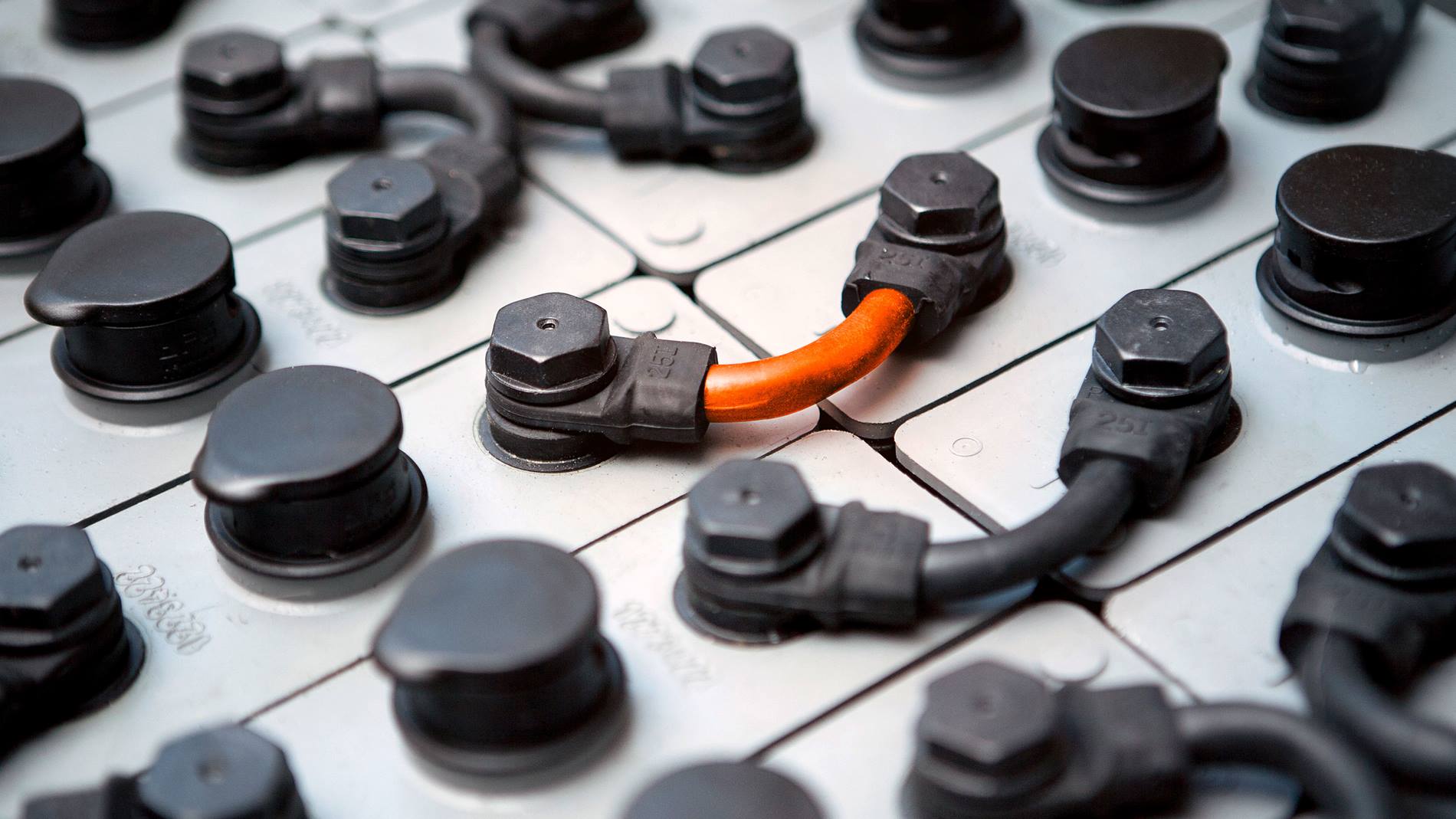
Automation in battery production
From the individual battery cell to the assembly of complete battery packs: With many years of expertise, KUKA covers the entire value chain in battery production systems and supplies corresponding automation solutions.
From planning to implementation and recycling: KUKA is contributing to the successful technological and economical implementation of innovations in the field of e-mobility
Everything you need for intelligent automation
Für jeden Kunden das maßgeschneiderte Konzept
Um eine maximale Expertise zu gewährleisten, stellen wir für jedes Projekt ein Team aus Spezialisten verschiedener Bereichen zusammen. Mit unseren effektiven Programmmodulen wie 3D-Simulation oder Offline-Programmierung lässt sich Ihre Batterie-Fertigung verlässlich planen, optimieren und im Voraus berechnen ohne die laufende Fertigung zu unterbrechen.
Wir erarbeiten holistische Lösungen und reagieren flexibel auf den dynamischen Markt:The right solution for every step of the value chain
Battery cell production

Battery module assembly
Assembly of battery packs
Inspection systems for module and pack lines
Cell-to-Pack technology
“Cell-to-Pack” (CTP) technology, also called “Module-to-Body” or “Cell-to-Body”, is a special process in the production of batteries for electric cars and other battery systems. The individual battery cells are assembled directly into complete packs and integrated into the end product. In this case, various fastening materials can be dispensed with and an increased energy density of the packs is possible. On the production and assembly side, KUKA provides support in the form of innovative developments within the production system in order to ensure that the respective battery designs are optimally inserted into the vehicle body. The broad technology portfolio enables, for example, the rotation of vehicle bodies so that cells can also be inserted and joined in positions that are difficult to access. KUKA already researches and develops corresponding solutions in the field of CTP, drawing on the experience gained in the manufacture of battery cells and the assembly of battery packs in electric cars.
Battery recycling
The need to develop cost-effective and sustainable concepts for reuse, recycling and raw material recovery is increasing, particularly in the global production of lithium-ion batteries. KUKA is actively involved in research in order to advise its customers on possible concepts for sustainable battery production and supply chain during the planning process. On the one hand, suitable battery designs and the right components can ensure that modules are dismantled without damage in a recycling facility designed and installed by KUKA and fed to a 2nd life cycle and re-use. Various technologies are combined to enable optimized disassembly of the packs. The other objective is to develop a disassembly-friendly design of the batteries together with our customers in order to achieve increased recyclability. Raw materials such as lithium, cobalt, nickel and manganese can thus be recovered more easily.