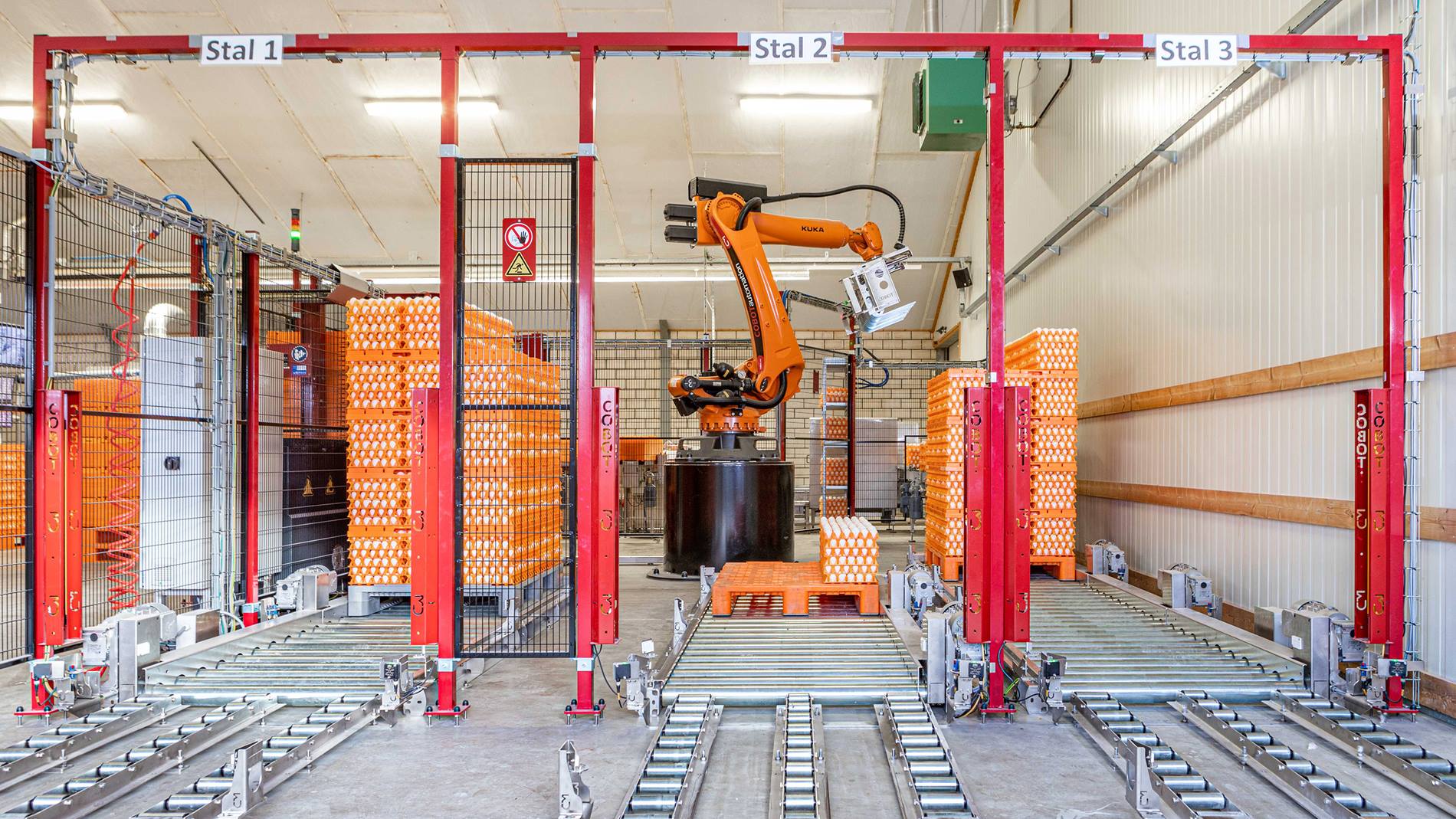
Fragile load: KUKA palletizer for chicken eggs
Farmers around the world automate egg palletizing with Meggson. The Dutch company designs and builds robot-based systems that prepare up to 108,000 eggs per hour for shipping – and protect the health of employees.
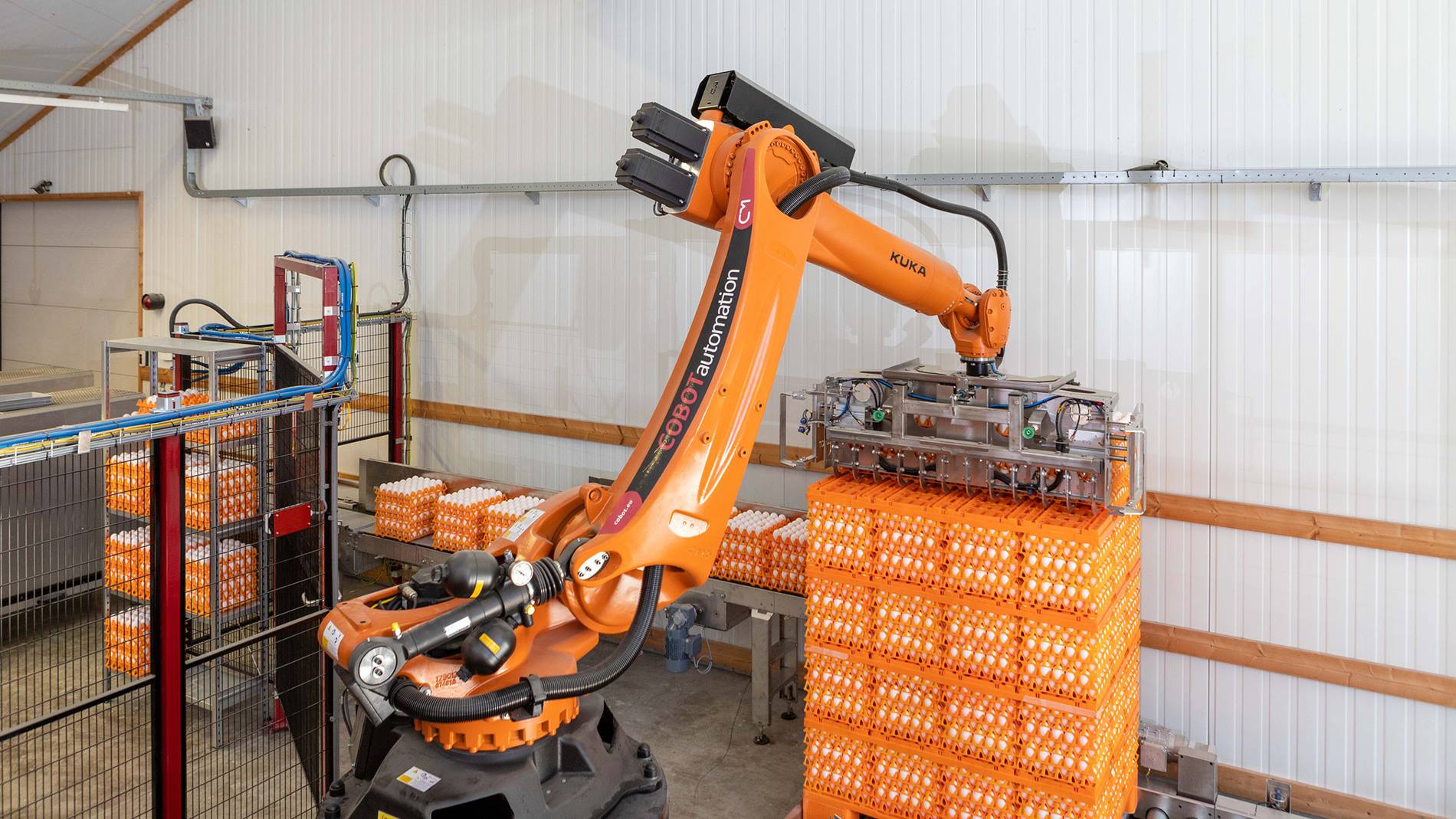
Palletizing system provides relief for employees

Palletizer scores high with special gripper

Up to 108,000 eggs per hour
The Meggson ROBOT TP300 automation solution can arrange up to 108,000 eggs per hour on pallets while placing the empty containers on a conveyor belt during the process. From here, the containers are transported away – either to be discarded or to be cleaned and refilled, depending on their condition. But Meggson automation solutions can do even more. Among other things, they impress in loading and unloading egg packing machines, palletizing cases full of eggs and handling setter trays. Moreover, they are compatible with all types of egg packing machines.

“If the farmers are happy, so are we”
For its flexible, high-performance palletizing systems, Meggson always has relied on KUKA robots. The integrator wants to provide the best possible support for farmers, and the 20 Meggson employees, in turn, feel optimally supported by KUKA. “That is the proverbial German quality,” Gijs Thomassen emphasized. “KUKA makes the best robots while also bringing many years of know-how – and that strengthens our trust in KUKA.”
“Working with KUKA palletizers is easy,” added Gerwin van de Geer, Product Manager at Meggson. “The first automation solution for eggs was still relatively complex to program. But once everything was up and running, we were able to replicate it time and time again.” The robots work with the KUKA KR C4 controller and after a brief introduction, customers usually can run it themselves. “KUKA designed a perfect program that our farmers can use comfortably,” van de Geer stressed. “That’s why they’re very interested in working with a system from KUKA. And if the farmers are happy, so are we!”
Simplifying strenuous processes thanks to a palletizing system
One of these satisfied customers is the Salomons Group, based in the Netherlands in the town of Dronten. Currently, more than 120,000 laying hens live on the Group’s associated farms. Since March 2020, the Group’s largest free-range farm has used a customized version of the ROBOT TP300 system. An employee checks and sorts fresh eggs from the coop so only intact ones end up on the conveyor belt. From there, the eggs are automatically arranged in egg trays. Via a conveyor belt, the egg cartons also reach the KR QUANTEC robot (type KR 120 R3100-2) in its cell. With its wide, stainless steel gripper, the KUKA robot picks up 12 full egg trays at a time in one fluid motion – three layers of four trays with 30 eggs each – and the layer palletizer carefully places them on the pallet. The entire process lasts 30 seconds, and the robot performs this step three times to complete one layer of the pallet.

Automatic palletizer – a sensitive powerhouse
The KR QUANTEC then places a separating layer on the eggs to secure the fragile cargo. Six layers of eggs – 6,480 in all – fit on a Salomons pallet. Between steps, the KR QUANTEC automatically moves empty egg trays to a second conveyor belt. From there, they can be transported out of the room and prepared for reuse.
In total, the system prepares 36,000 eggs for shipment each hour – and does so with maximum reliability and minimal risk of breakage. In the past, two to three employees worked in unison here to load pallets. Now, one of them has taken over quality control, and the others have found less physically demanding tasks on the poultry farm.

No egg is lost
“We at the Salomons Group love to find solutions that simplify processes,” stated Klaasjan Salomons, Managing Director of the family-run business. Salomons also notes that the company used KUKA palletizing robots and enjoyed working with Meggson even prior to its most recent automation project. However, Klaasjan finds that the new palletizing system does even more. For one thing, Salomons appreciates that “when a coop is changed, the leftover eggs that do not completely fill a tray can be stored temporarily on the pallet. These are then transported onward the next day.” No egg is forgotten or lost.

Working with KUKA palletizers is easy. The first automation solution was still relatively complex to program. But once everything was up and running, we were able to replicate it time and time again.
Scope for innovation and expansion
In an expansion phase, The Salomons Group is building a facility in Ghana, where chicken eggs are very expensive. For many people in Ghana, a professional layer poultry farm represents the chance to feed their families. The team at Meggson is happy to help free up resources for entrepreneurs like the Salomons family so they can plan and implement projects like these. For Gijs Thomassen, this is an incentive to keep developing his own automation solutions for layer poultry farms. This is because “they improve working conditions for employees and, at the same time, enable better control of egg palletization – which increases output quality.”
