
Robot with camera supports assembly process at household appliance manufacturer
At domestic appliance manufacturer Miele, a KUKA KR 20 robot automates the production of drive motors for household tumble dryers. The KR 20 works largely autonomously thanks to the camera system.
Attention, this area is under camera surveillance! This motto applies exactly to production operations at household appliance manufacturer Miele following implementation of a robot with a camera system at the company. The KUKA KR 20 robot can perceive its environment precisely, allowing it to react flexibly to new situations and operate with an increasing degree of autonomy. This demonstrates how autonomous robot systems give rise to entirely new application potential in the automation of production.
Robot with camera offers great flexibility
The palletizing system at the Euskirchen plant of Miele & Cie. KG in western Germany was planned and implemented jointly by the companies Heinen Automation GmbH & Co. KG and ID Ingenieure & Dienstleistungen GmbH. It features a camera-assisted KUKA robot which feeds components to the production process. The decisive criterion for Miele was the flexibility of the handling application. The robot had to be capable of handling a range of different components.

It was Miele’s explicit wish for an individual handling application to be implemented that could be quickly and easily adapted to different components and assembly processes
KR CYBERTECH inspects components for defects
A KUKA KR 20 robot from the KR CYBERTECH series is the centerpiece of the application. “The robot has the task of feeding partly sorted stators automatically to the assembly process,” summarizes Michael Miessen. Stators are components of electric motors and are required for the drive motors of household tumble dryers. The highlight: the robot gripper is equipped with a camera. This checks both the quantity of components to be processed and their exact position. The inspection is necessary since the components are liable to be displaced by several centimeters on account of jolts during transportation. With the aid of the camera, the deviations can be detected and the stators autonomously picked up by the robot gripper without manual assistance.

High expectations met 100 percent
After the inspection, the robot gripper is positioned over the component and picks it up. The KR 20 subsequently places it in a turnover station. A handling gantry then takes over, positioning the stator in the parts carrier. When all the small load carriers are empty, the robot stacks them on the outgoing roller bed. The pallets are finally conveyed out of the system.

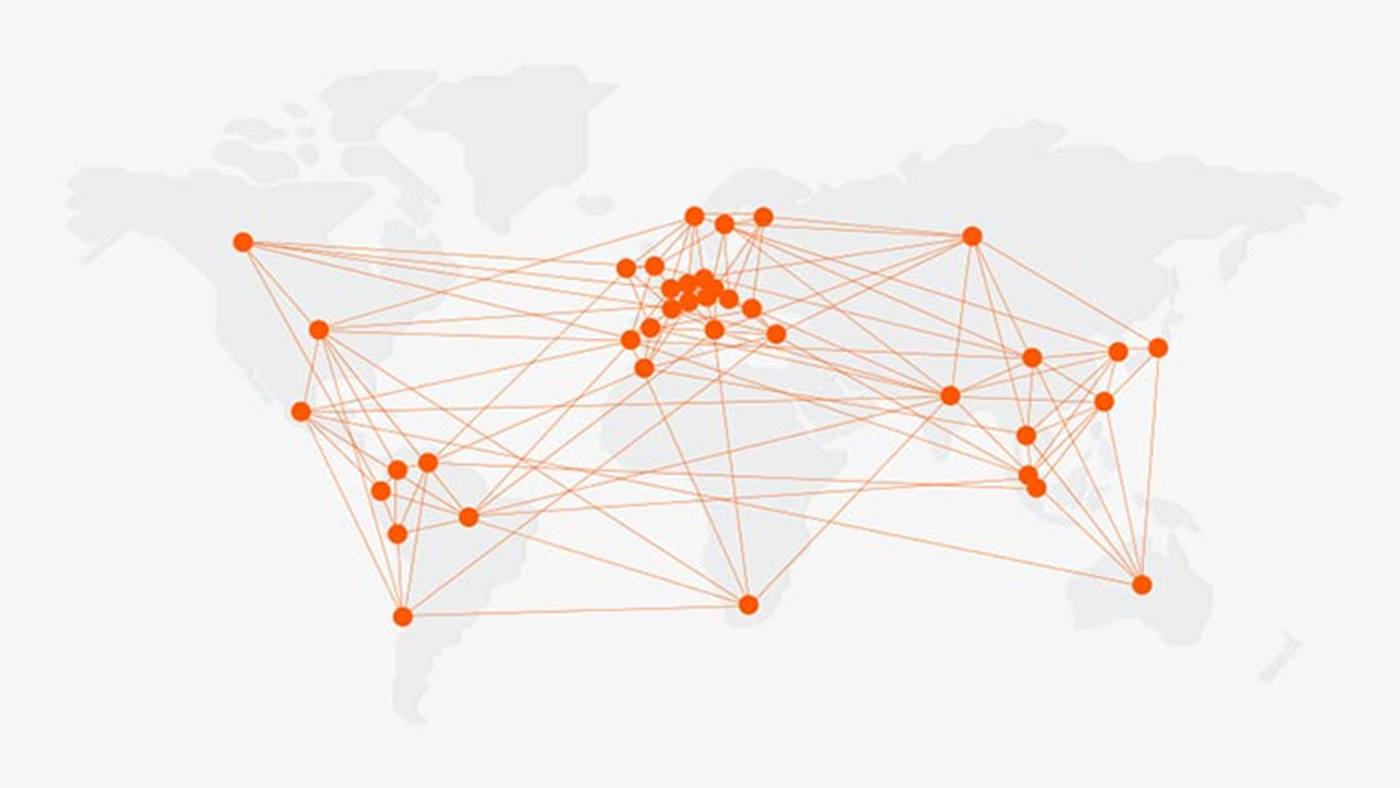