Industrie 4.0 in practice: references and success stories
KUKA is playing a decisive role in driving the digital transformation forward. Within the framework of partnerships, KUKA is pursuing clear goals: to prepare industrial production for challenges and applications that are unknown today – and to do so as tangibly as possible.
KUKA and SAP: Industrie 4.0 in ongoing production
The positive effects of digitalization become apparent at times of crisis. If a machine or an industrial robot unexpectedly suffers damage or stops, if the performance is no longer right or if supply chains break down, collaboration with overarching software systems is required in order to resolve the problem. This is where SAP comes in as a software system vendor.
Using a manufacturing cell in KUKA’s in-house machining department, we demonstrate together with SAP how industrial digitalization can succeed. An SAP Asset Intelligence Network (SAP AIN) implementation with a KUKA robot takes place in a real production environment. The goal is to prepare industrial production for challenges and applications that are unknown today through the targeted collection and evaluation of data.


KUKA in the Open Industry 4.0 Alliance
To ensure that the digital transformation in Europe is not slowed down by stand-alone solutions and incompatible standards, the machinery in all the highly automated factories and systems must speak the same language: what is needed is a vendor-neutral, standardized ecosystem that is open to all and also integrates logistics and services. The Open Industry Alliance was founded in 2019 precisely for this purpose. Renowned companies from the fields of mechanical engineering, industrial automation and software have joined forces here to develop a so-called Open Industry 4.0 Framework – and KUKA is at the forefront. Each member of the alliance provides its core competencies to standardize areas such as connectivity, data management, IT security and cooperation opportunities. And industry across Europe benefits from an open, standards-based, and compatible offering for the entire spectrum from an object in the production shop to service.

KUKA robots in the LEGO cloud
Research is essential for KUKA. This also includes constant cooperation with universities and renowned institutes around the world. One of our research partners is Aalborg University in Denmark. Here, a research team wanted to show how easily various machines in a production shop could be connected to the cloud. The researchers simply used the open reference architecture of the Open Industry 4.0 Alliance of which we are a co-founder. For example, they were able to connect a KUKA robot to the Lego Group’s Microsoft Azure cloud via an edge interface from our subsidiary Device Insight. Two infeed stations, a manual station and a KUKA robot cell were combined to form a small, smart production line that can individually assemble and package LEGO bricks.

Global remote service platform from Device Insight
Krones is a leading manufacturer of process, filling and packaging systems. Customers who opt for a Krones system are making a major investment and therefore rightly expect fast and reliable customer support. KUKA subsidiary Device Insight supplied Krones with a global remote service platform based on CENTERSIGHT®.
Krones service technicians can use this to connect to all of the more than 20,000 systems worldwide – right down to the control level of individual components.
Krones customers simply authorize the time frame and access to their system by e-mail or at the push of a button. When the remote service process has been started, Krones documents every activity performed in CENTERSIGHT®. In this way, Krones customers retain full control, transparency and legal certainty – and Krones gains an overview of all processes on any given machine. Last but not least, CENTERSIGHT® also ensures greater sustainability. This is because Krones technicians now only have to travel to the customer’s site if it has been clarified in advance via remote service whether it is really necessary.

KUKA test facility with 5G
For many modernization requirements, previous wireless technologies such as WLAN or 4G are not sufficient: the transmission rates are too low and it is possible that security-relevant data will not arrive quickly enough. However, the new 5G standard combines the high bandwidth required for production with the necessary reliability. Currently, 5G for industry is still at the development stage.
However, KUKA is already working toward ensuring that 5G replaces existing wireless technologies in the long term. For example, we have equipped our “Smart Production Center” test facility in Augsburg with 5G technology. Several mobile platforms connected with 5G make it possible for the facility to manufacture a wide variety of products – from washing machines to bicycle frames to car body parts.

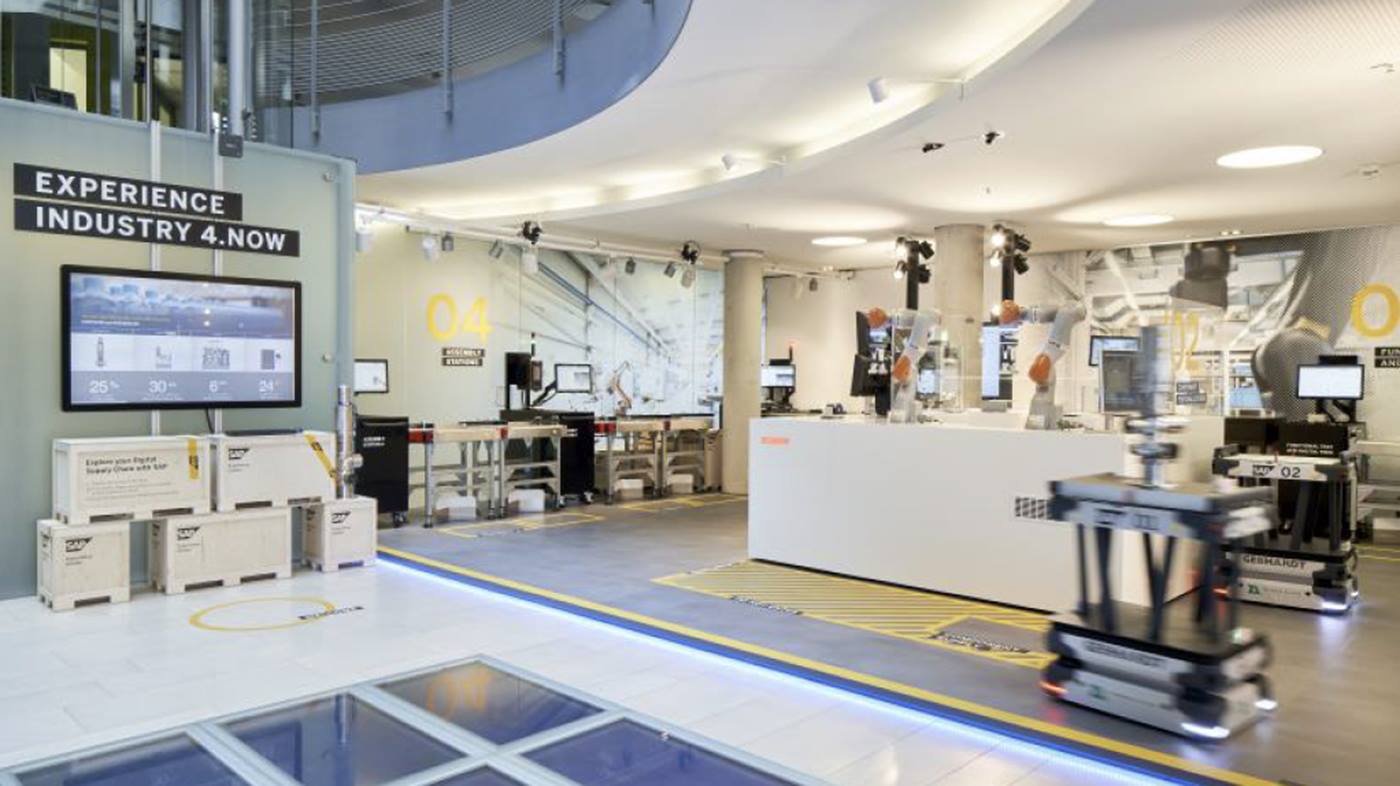
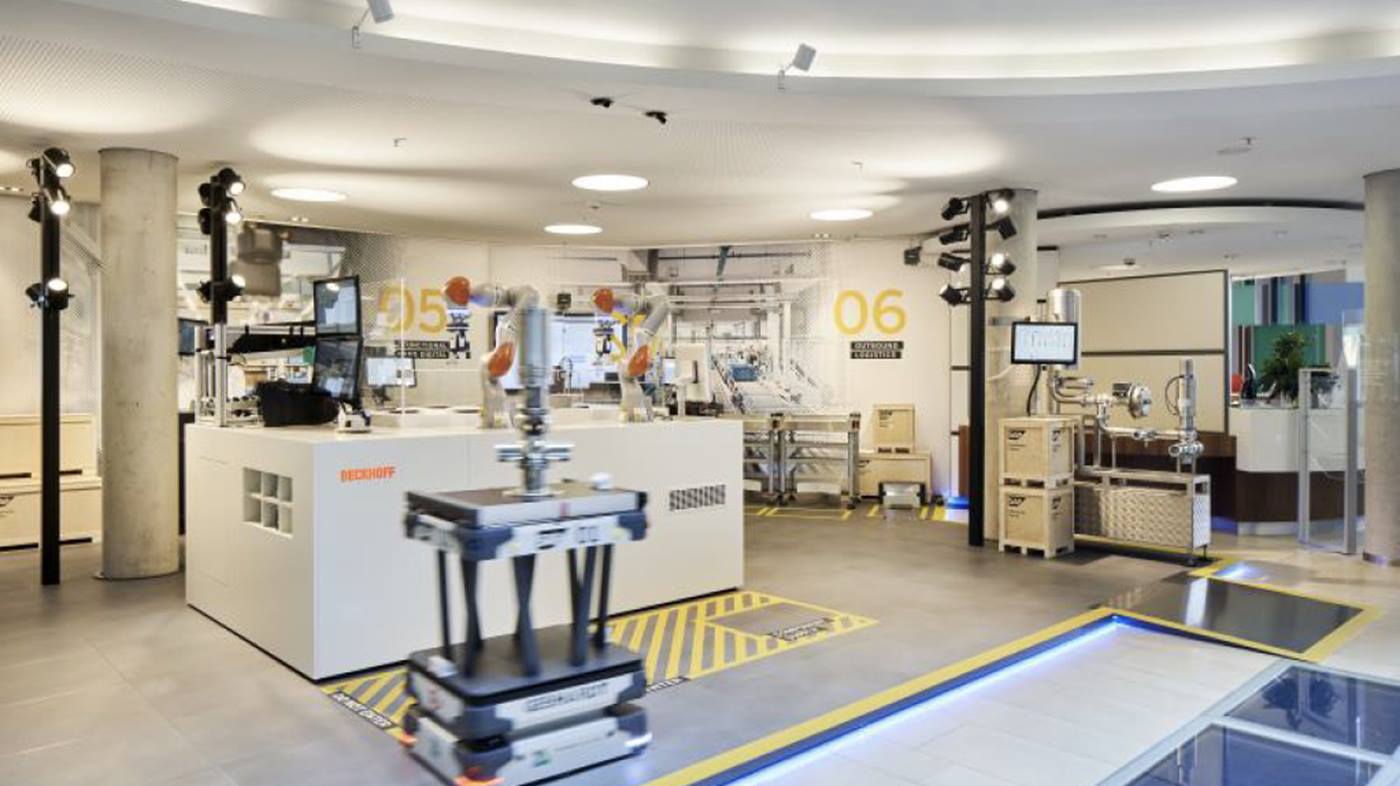
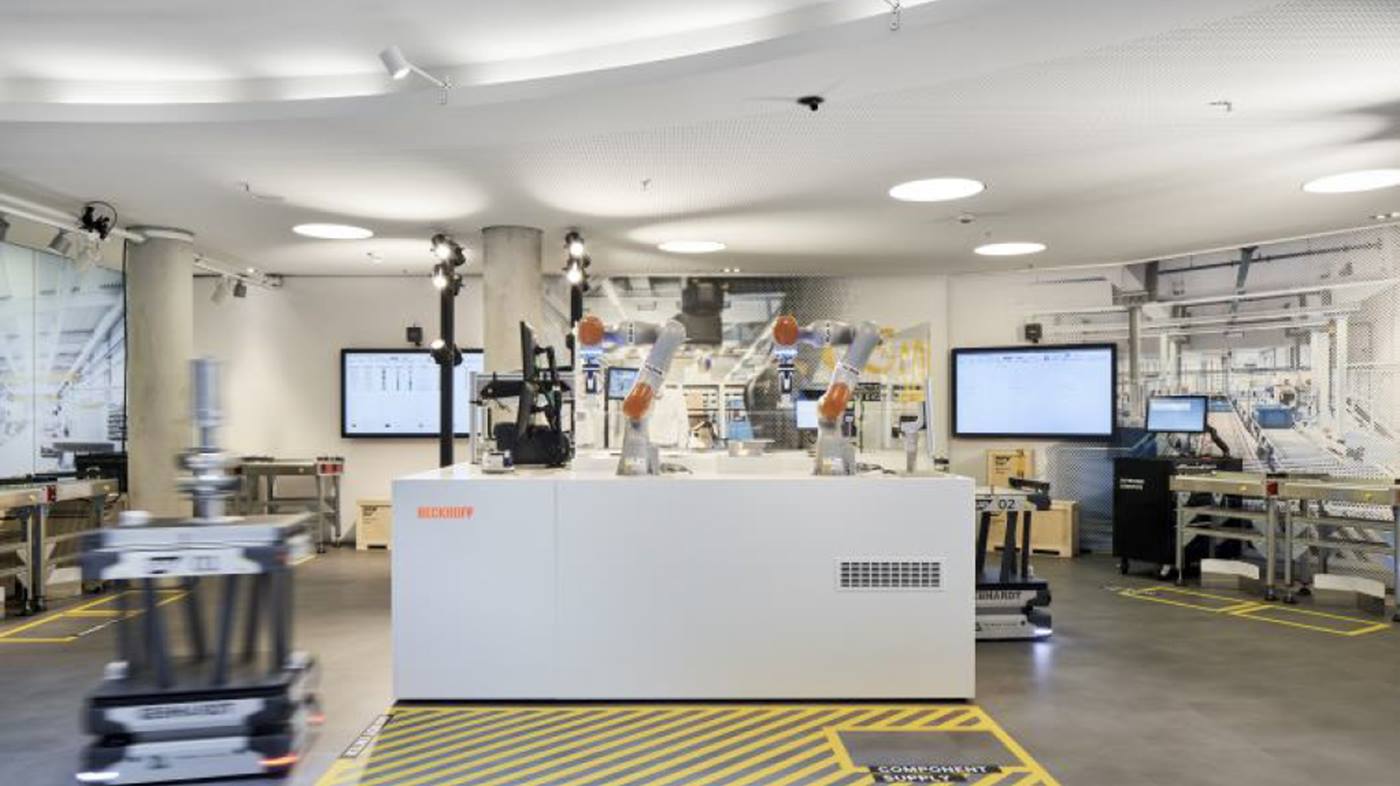
KUKA connects
A KUKA robot works seamlessly with machining centers from another manufacturer: no problem thanks to the KUKA SmartProduction environment, which is implemented in one of our use cases, for example. In a fully automated and connected robot cell, our robot picks up castings with its pneumatic grippers from Zimmer and transfers them to a machining center from Heller. Here, the parts are drilled and milled. The robot then unloads and deburrs them. In order to enable it to tend a second machining center as well, it is installed on a linear unit that gives it a full range of motion.
The collaboration works so smoothly because both our robot and its grippers and the Heller machining centers and all other components are connected to each other and to the KUKA Cloud. Products from other manufacturers can thus be easily integrated into the SmartProduction environment. In the KUKA Connectivity Box, all data are collected and transmitted to the cloud. A clearly structured dashboard gives operators and management an overview of all components and full control over the entire production process.
