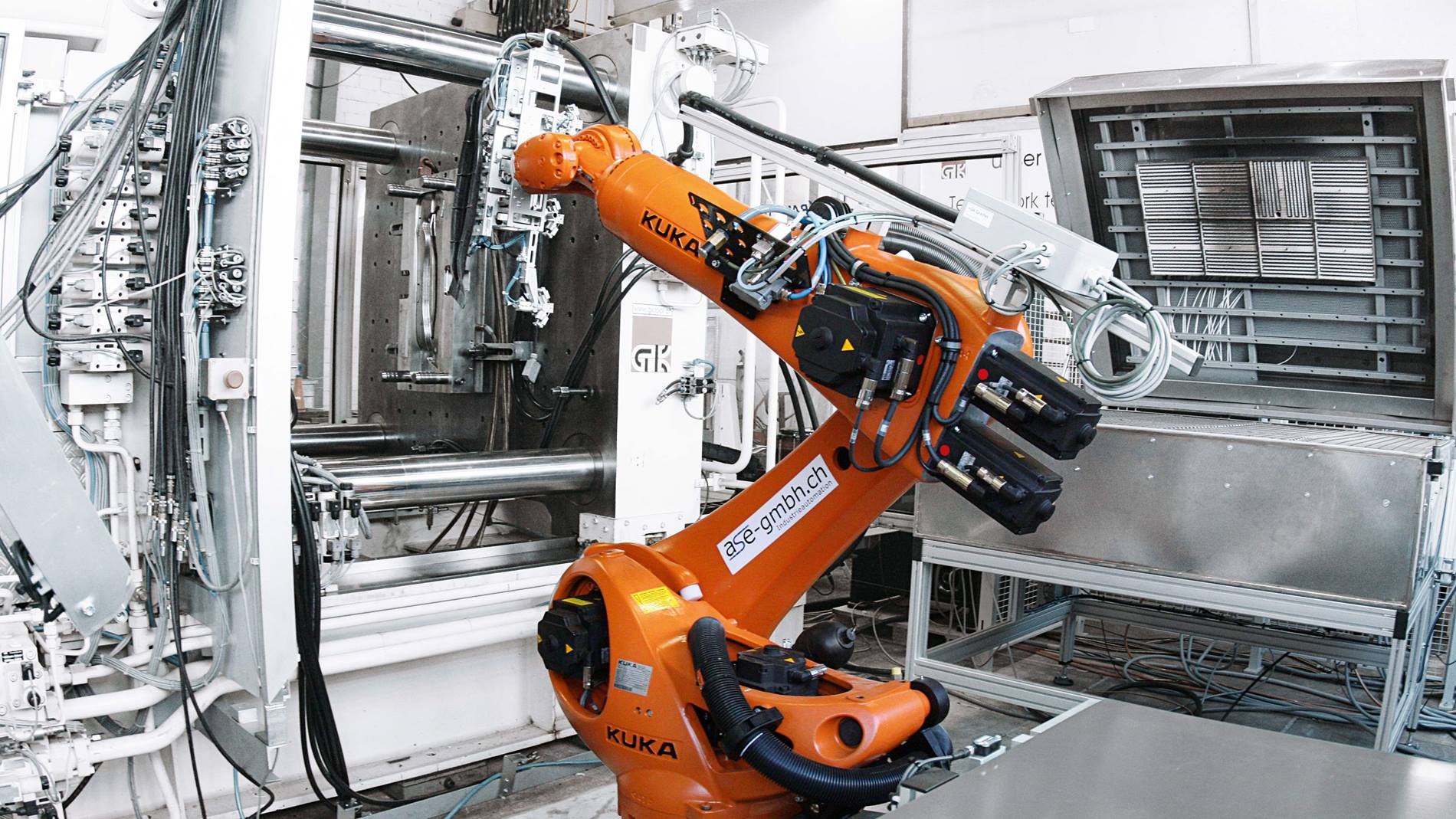
En KUKA, dos máquinas-herramienta fabrican 14 módulos diferentes para y con robots KUKA
El desarrollo, la producción y la venta de robots industriales, unidades de control y software: KUKA Roboter GmbH, con sede en Augsburgo, es uno de los líderes del mercado mundial
También en la fabricación propia de robots, la empresa de Augsburgo apuesta por la automatización. La última automatización basada en robots realizada en dos centros de mecanizado (BAZ) en la nave 10 ha provocado un aumento medio de la productividad de más de un 15 %.
Componentes para la fabricación de robots KUKA
En la mecanización que se lleva a cabo en esos centros, se fabrican componentes que se usan en la fabricación de los robots de KUKA en una superficie de 3.000 metros cuadrados. Desde el año 2013 hay dos máquinas-herramienta DMG MORI del modelo Sprint 65-3 (denominación corta: Sprint) y CTX beta 1250 TC-4A (denominación corta: CTX) que, a partir de piezas de fundición y tramos serrados, fabrican 14 componentes que a continuación se usan en el montaje de robots colindante.
Solución de automatización muy flexible
La solución de automatización se caracteriza por una flexibilidad muy elevada en el espacio más reducido. Mediante el sistema de alimentación de componentes KS CycleMove de KUKA Systems GmbH las células ganan en capacidad de adaptación. Además, mediante el almacenamiento de reservas de los componentes, se obtiene el tiempo de servicio máximo sin personas de hasta ocho horas. Mientras la instalación Sprint, un torno automático de giro, crea componentes para los robots a partir de tramos serrados en pocos minutos, el torno automático de mecanización CTX de al lado mecaniza piezas de fundición y tramos serrados en un tiempo de ciclo de aprox. 30 min.
En la instalación Sprint se fabrican actualmente siete componentes, la gama de piezas abarca desde un perno para la serie KR QUANTEC con un diámetro de 55 mm hasta una brida para los robots de carga pesada de la serie KR FORTEC con un diámetro de 120 mm. Con la CTX también se fabrican siete piezas, estos componentes se convierten, entre otros, en carcasas de ruedas dentadas para el KR AGILUS y el KR QUANTEC con un diámetro correspondiente de 95 mm hasta 246 mm. A través de varias pistas de alimentación y retorno, los centros de mecanizado pueden trabajar de forma autónoma con un servicio de tres turnos.
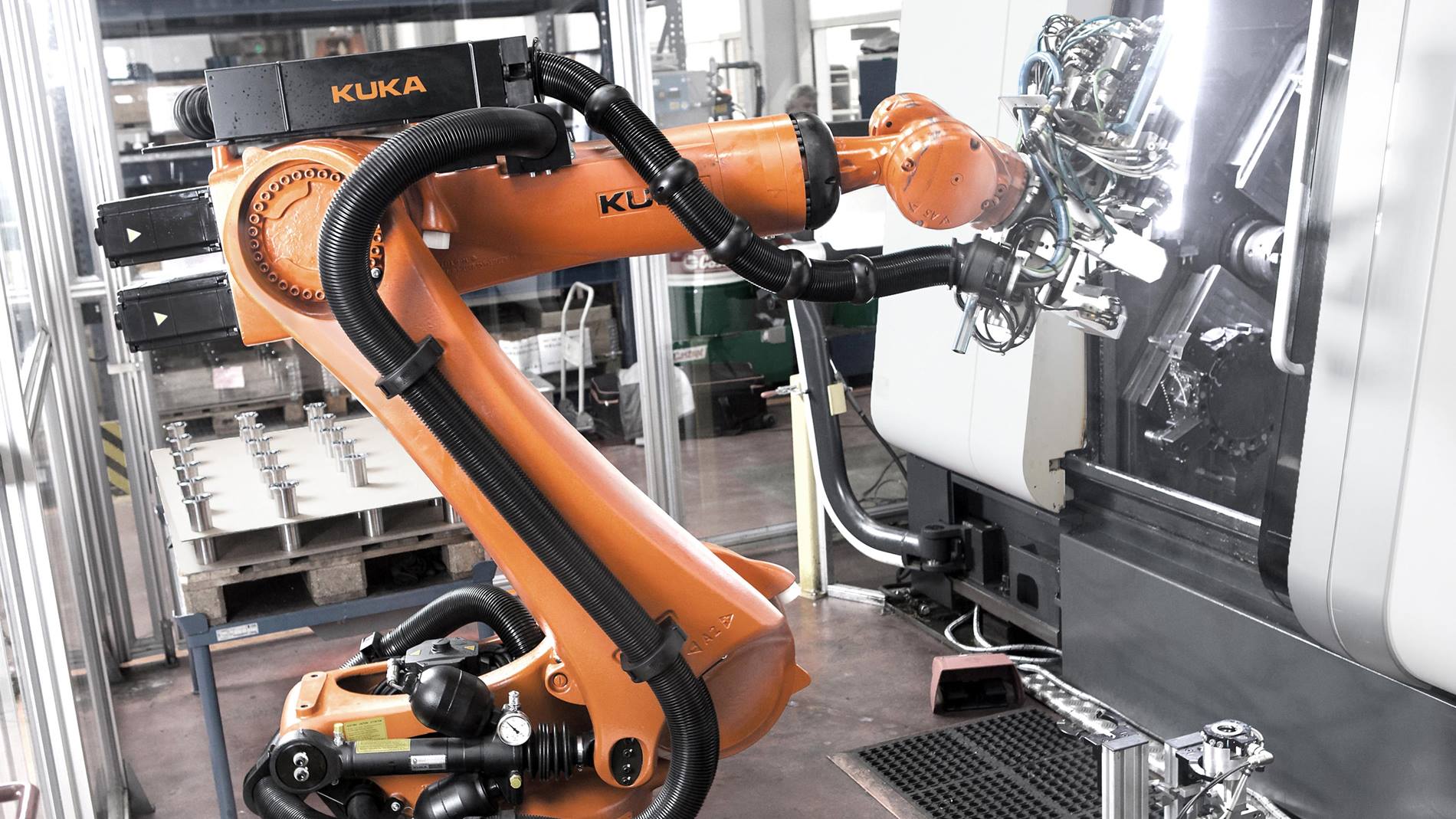
Esfuerzo de transformación reducido y posibilidad de ampliación
