
Assembly line work 4.0 – thanks to KUKA palletizing robot
A fully automatic palletizing system, in which a KR QUANTEC PA from KUKA stacks the boxes, ensures satisfaction at an Australian company for body care products. The palletizing robot supports employees efficiently and safely in the heavy physical work – and does so at a constant speed and without tiring. The system was installed by KUKA systems partner Scott.
Fully automatic stacking with palletizing cell

Reliable partner for robots and palletizing systems

KR QUANTEC offers versatility in stacking

Palletizing system from KUKA as a cost-saving solution
Full productivity with no breaks
The automated palletizing also ensures that the boxes stacked on top of each other are positioned evenly to avoid products falling off or pallets being loaded lopsided. Furthermore, the palletizing cell operates at a constant speed, without a break or interruption. The customer is highly satisfied with this system offered by Scott and KUKA. The requirements – lower production costs, reliable handling of different stacked boxes and greater safety for employees – were met in full.
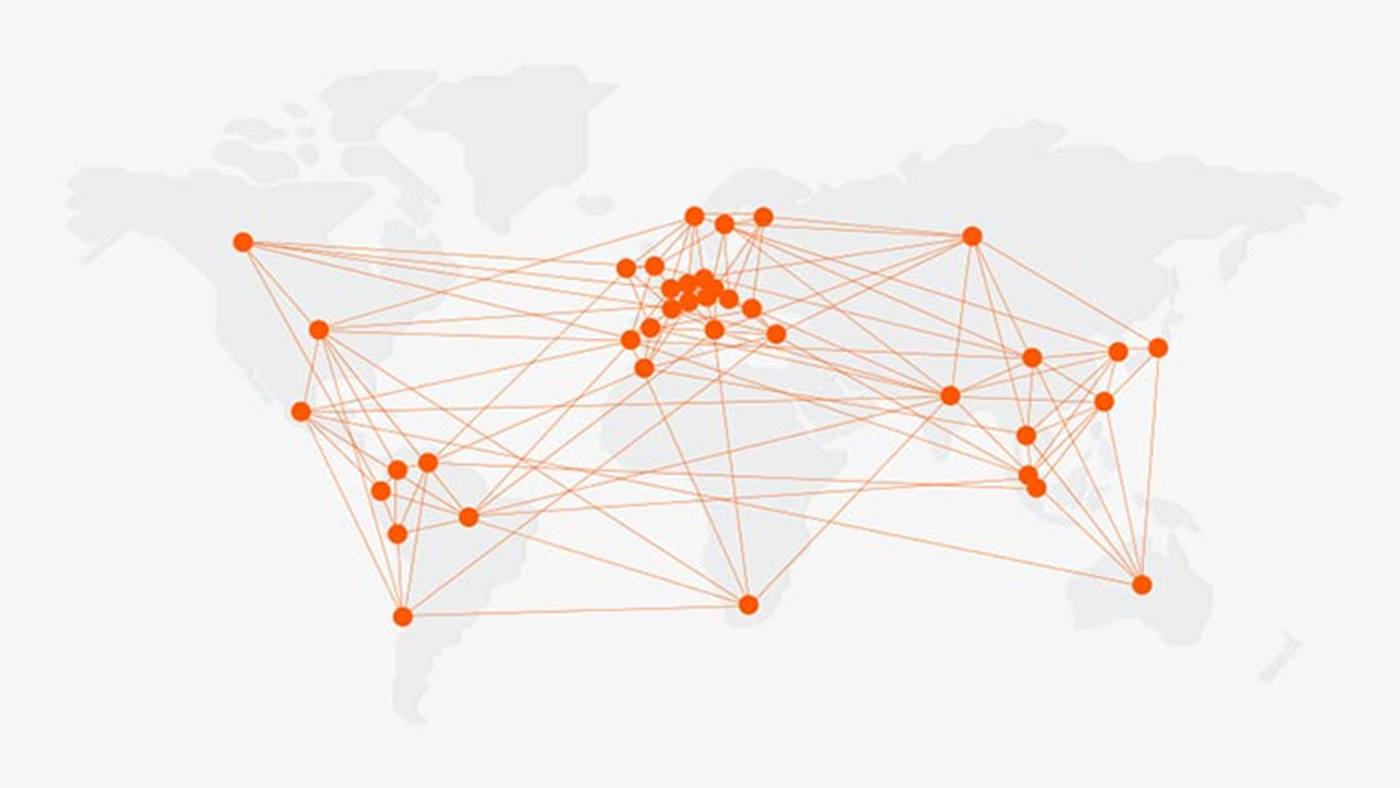