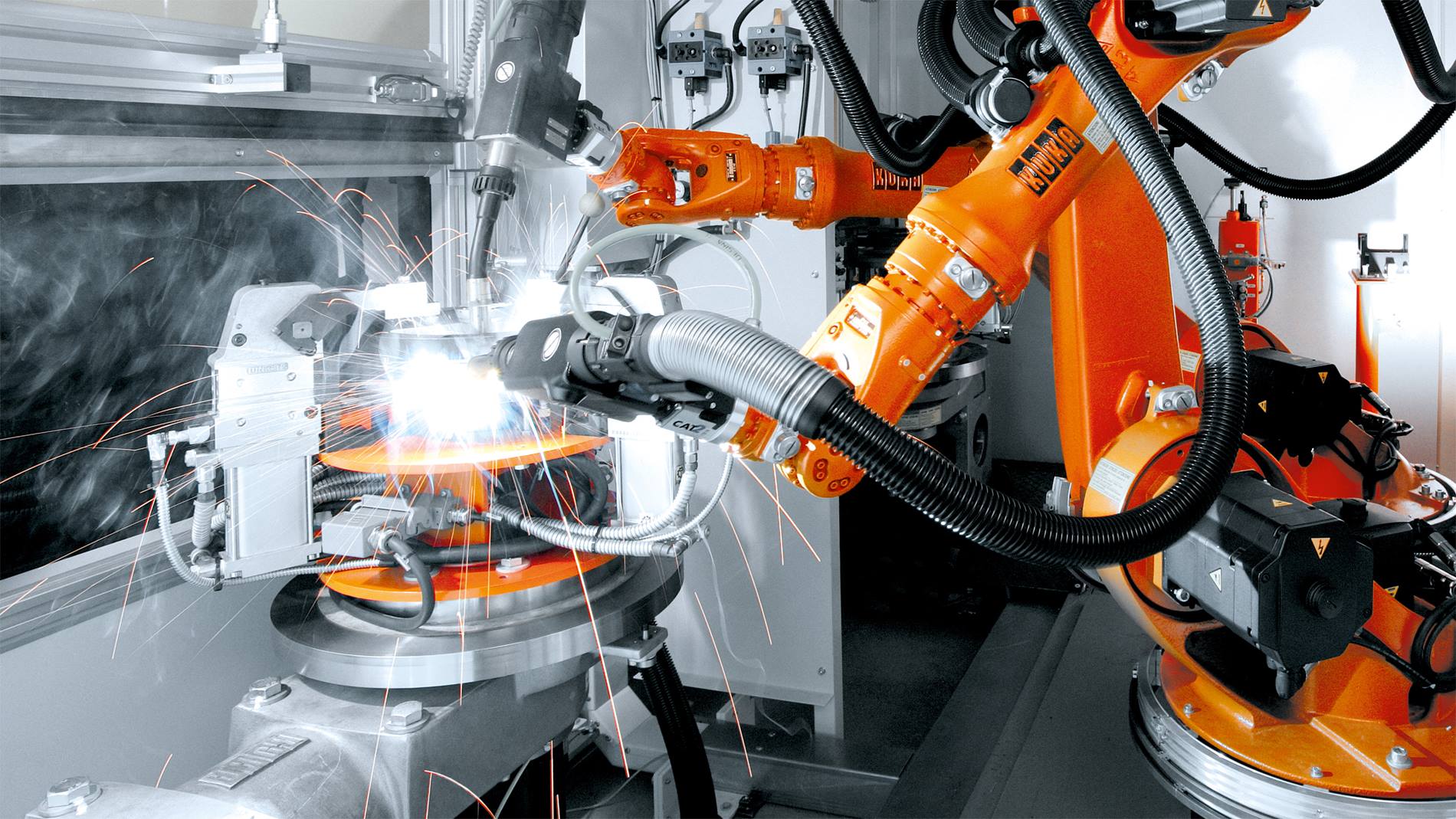
Automated arc welding
Arc welding is the most widely used joining process. KUKA provides many automation components, function packages, robots, and cells. These standard products are easy to use and available quickly. From MIG welding to MAG welding and on to TIG welding.
Learn about the different arc welding processes
Gas metal-arc welding is an arc welding process in which an electric arc is ignited between an electrode and the component, fusing the components and, if applicable, a filler metal. Here, a distinction is made between several methods. Among these, MIG/MAG welding and TIG welding are the most used methods for the process. These differ in the type of gas that is used and the choice of materials. They impress with maximum weld quality and a high weld speed.
MIG/MAG robot welding
MIG/MAG welding is an arc welding process in which an electric arc is ignited between a welding wire and the component, fusing the components and the filler metal. To protect the weld pool from the reactive oxygen in the environment, a shielding gas is supplied with the welding wire. This displaces the oxygen at the welding point and thus prevents oxidation of the weld pool.
In metal active gas welding (MAG), an active gas, such as CO2 or a CO2 mixture, is used. The active gas reacts with the weld pool and stabilizes the arc.
Metal inert gas welding (MIG) uses an inert – i.e. non-reactive – gas such as argon or nitrogen.
Advantages
-
High weld speed
-
High deposition efficiency
-
Inexpensive
Application
-
MIG: alloyed and unalloyed steel
-
MAG: precious metals such as stainless steel, aluminum, titanium or copper
TIG robotic welding
In tungsten inert gas welding (TIG), also known as gas tungsten arc welding (GTAW), the welding current is supplied through a tungsten electrode, which is temperature-resistant and does not melt. As in MIG welding, inert shielding gases (such as argon or helium) are used to prevent a reaction with the oxygen in the air. If a filler metal is required for a specific application, it is fed separately via an external wire feeder.
Advantages
-
Excellent seam quality and appearance
-
Suitable for all weld positions
Application
-
All weldable metals
-
Thin-walled components
Plasma welding
Plasma welding is a variant of TIG welding in which the arc is constricted by a water-cooled nozzle. In addition, a plasma gas, usually argon, also flows between the electrode and the nozzle, is introduced to create a plasma that has a greater power density than the arc robot alone. Plasma welding process employs a copper nozzle and the electrode is tungsten 2 % thoria. The diameter of the eletcrode tip is not as critical as for GTAW. It should be maintained around 30 to 60 degrees.
Advantages
-
Greater power density
-
High-speed metal arc welding
-
Low distortion
-
Can be combined with external wire feed
Application
-
Micro-plasma welding (0.1 - 1 mm workpiece thickness)
-
Plasma welding with keyhole (3 - 9 mm)
-
Plasma MIG welding (3 - >10 mm)
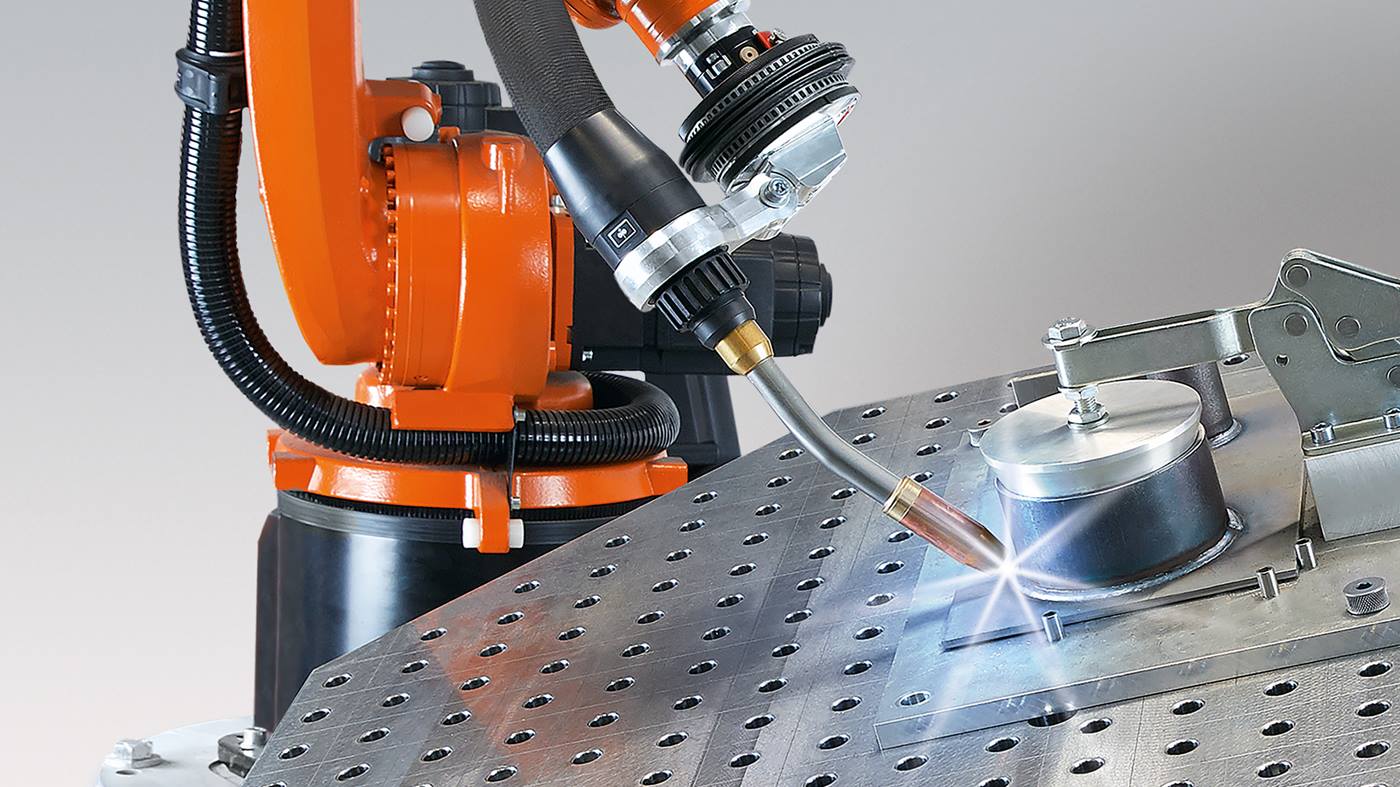
Welding robots, positioners and welding cells:
Standardized modular components that can be ideally combined
Software and sensor technology – no matter how complex the welding task
- KUKA.ArcTech: welding software with many functions for easy and fast operation and programming of the welding application
- KUKA.TouchSense: software for seam search and detection of shape and position deviations of metal components
- KUKA.Sim: even more efficient offline programming with the KUKA.Sim ArcWelding AddOn for arc welding applications
- KUKA.ProcessScreen: software for the monitoring and documentation of process parameters
- KUKA.SeamTech: software for the integration of sensors for seam finding and seam tracking as well as correction of robot motion during the welding process
- KUKA.TRACC TCP: software technology package for automatic checking and calibration of the torch TCP in the production cycle
- KUKA.iiQoT is a central IIoT platform for data-based automation
- KUKA.AppTech offers predefined structures and program sequences for fast start-up of your welding application and provides modules for structured communication between the industrial robot and the programmable logic controller (PLC)
Cooperation with major manufacturers of welding equipment
KUKA robots achieve the best welding quality with the appropriate welding equipment from our strong partners such as Binzel, ESAB, EWM, Fronius, Kemppi, Lincoln, Lorch, Megmeet, Migatronic, Miller or SKS.
The robotic arc welding equipment is easily and quickly connected to the robot controller via a field bus interface, such as EtherCAT. In this way, the full range of functions is available to the welder at all times.

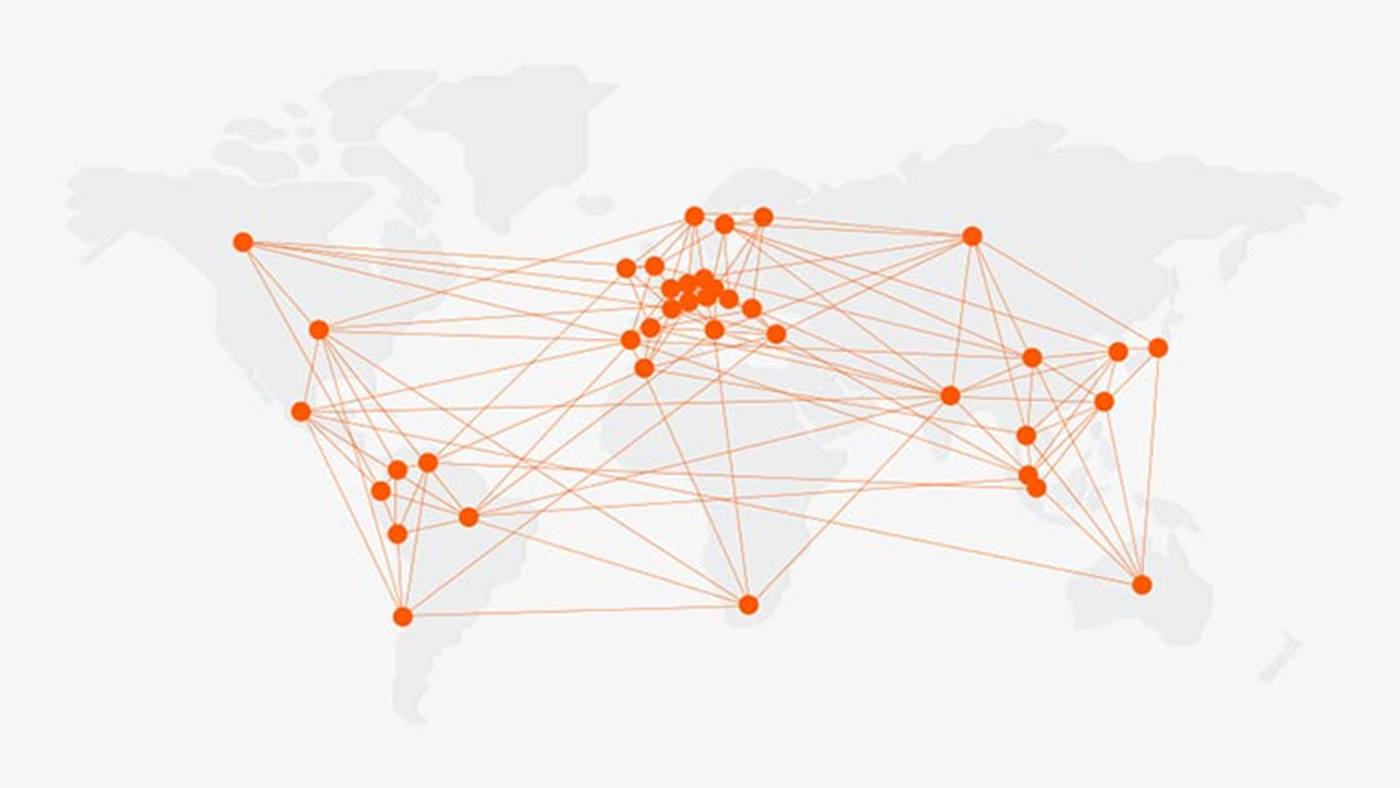