
Zhongli North America, Inc. Forges Strong Bond with KUKA
As Zhongli set up its Shelby Township, Michigan plant, it faced the challenge of maintaining high precision and volume in automotive parts production. With KUKA’s advanced welding robots and intuitive software, Zhongli successfully automated its welding and material handling for complex assemblies of automotive components.
With its parent company and all previous manufacturing established in Shanghai, Zhongli elected to bring production of chassis components, primarily those related to noise, vibration and harshness (NVH) performance, to North America for OEM manufacturers.
Zhongli Brings Production to North America
Given the scale of its production and the precision required for its parts, there was no alternative to automating Shelby Township, Michigan’s Zhongli North America, Inc. manufacturing plant’s welding cells. The Tier 1 auto chassis component manufacturer has been fine-tuning its KUKA-driven automated welding process for the better part of 2024, since beginning North American operations in 2023.

Given the scale of its production and the precision required for its parts, there was no alternative to automating Shelby Township, Michigan’s Zhongli North America, Inc. manufacturing plant’s welding cells. The Tier 1 auto chassis component manufacturer has been fine-tuning its KUKA-driven automated welding process for the better part of 2024, since beginning North American operations in 2023.
Manufacturing Cell for Automotive Control Arms
Zhongli needed to automate the MIG welding and material handling system to produce an automobile control arm. The control arms are built by welding three components with four welds. Four robotic welders operate between two fixtures and perform 16 welds simultaneously to form four control arms.
Welding with Robots
KR CYBERTECH nano ARC HW robots are tasked with the precision welding, providing extremely fast and precise continuous-path motion. The six-axes robot uses a hollow-wrist construction for reduced main axis motion with repeatability of 0.04 mm. The KR QUANTEC tackles the material handling duties within the cell, moving the components and fixtures with an accuracy of 0.06 mm.

Intelligent Workflow
KUKA’s automated cell provided economic, logistical and safety solutions in addition to producing the desired manufacturing results. The KR QUANTEC robots eliminated the need for human material handlers to move parts and fixtures between stations. Operators within the cell would slow the process dramatically, require a larger cell footprint and pose inevitable safety issues caused by people moving in and about live robotic welders.

Intuitive Software
Zhongli uses KUKA.ArcTech, an intuitive modular welding software package that controls all essential welding tasks. The software allows operators to program and optimize weld parameters regardless of whether the power source is a MIG/MAG, TIG or plasma device. Overall cell development and material flow was developed using KUKA.Sim, allowing Zhongli engineers to optimize processes virtually outside the production environment. Digital cell development and simulation allowed Zhongli to refine its processes with minimal cost and effort, which is essential when bringing a complex application online.

Forging a Partnership
“KUKA has performed very well,” said Kyle Fleeger, Zhongli manufacturing and maintenance engineer, who has been actively testing and tweaking the cell since it went into operation. “We’ve done many trials on gas types, wire types, different diameters and thicknesses, and we’ve been able to make these changes the same day. KUKA has been very incorporative of the different styles and trials that we try to achieve a better product.”

KUKA has been a great partner through this process, and we’re looking forward to continuing that relationship.

Support and responsiveness was instrumental in commissioning the cell quickly and getting parts to customers.
“One of the issues we originally had was customer timing, and that was a huge benefit that KUKA gave us,” Valitutti said. “KUKA had a much shorter lead time for the robots than anyone else we could have potentially looked at.”
“Additionally, we had a lot of the typical issues you encounter when bringing a system like this online, but we were able to get through them quicker than we probably would have with any other company,” Valitutti said.
“Additionally, we had a lot of the typical issues you encounter when bringing a system like this online, but we were able to get through them quicker than we probably would have with any other company,” Valitutti said.

Providing a First-Class Product
From a shop floor view, Fleeger said KUKA’s precision, reliability and overall high quality provide a solid manufacturing base to produce a first-class product.
“This automation allows us to achieve the critical characteristics in our products that our customers require,” Fleeger said. “Even with its complexity, KUKA automation brings a certain simplicity. It allows you to understand how it’s controlled and how to modify it to incorporate what you need and want to do to make a better product.”
“This automation allows us to achieve the critical characteristics in our products that our customers require,” Fleeger said. “Even with its complexity, KUKA automation brings a certain simplicity. It allows you to understand how it’s controlled and how to modify it to incorporate what you need and want to do to make a better product.”

Just the Beginning
As far as Valitutti is concerned, the Shelby Township manufacturing plant’s welding cells are just the beginning of the company’s future automation strategies. “We’ve started discussions about automating some of our very manual processes, and we have high hopes of automating a lot of what we do here,” Valitutti said.

More about the KUKA partner
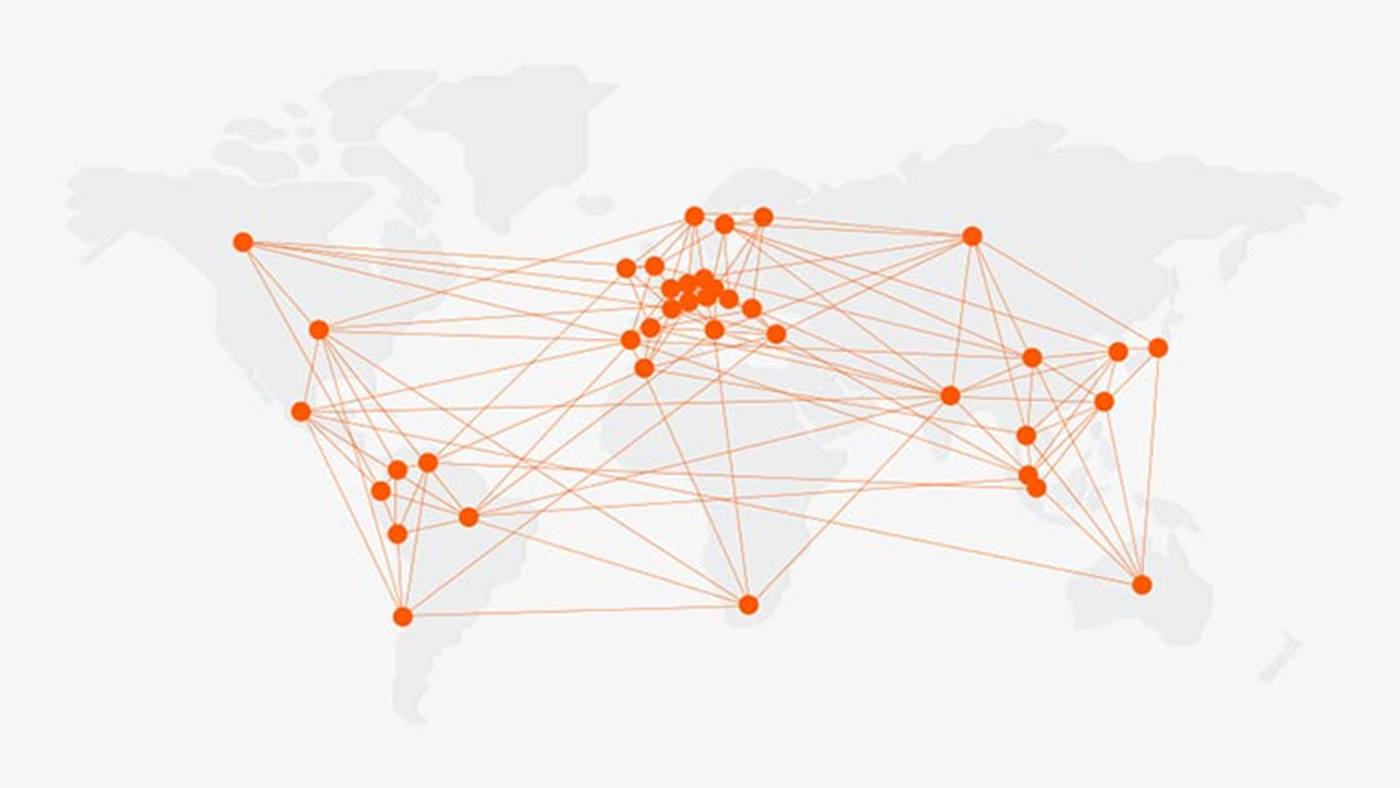