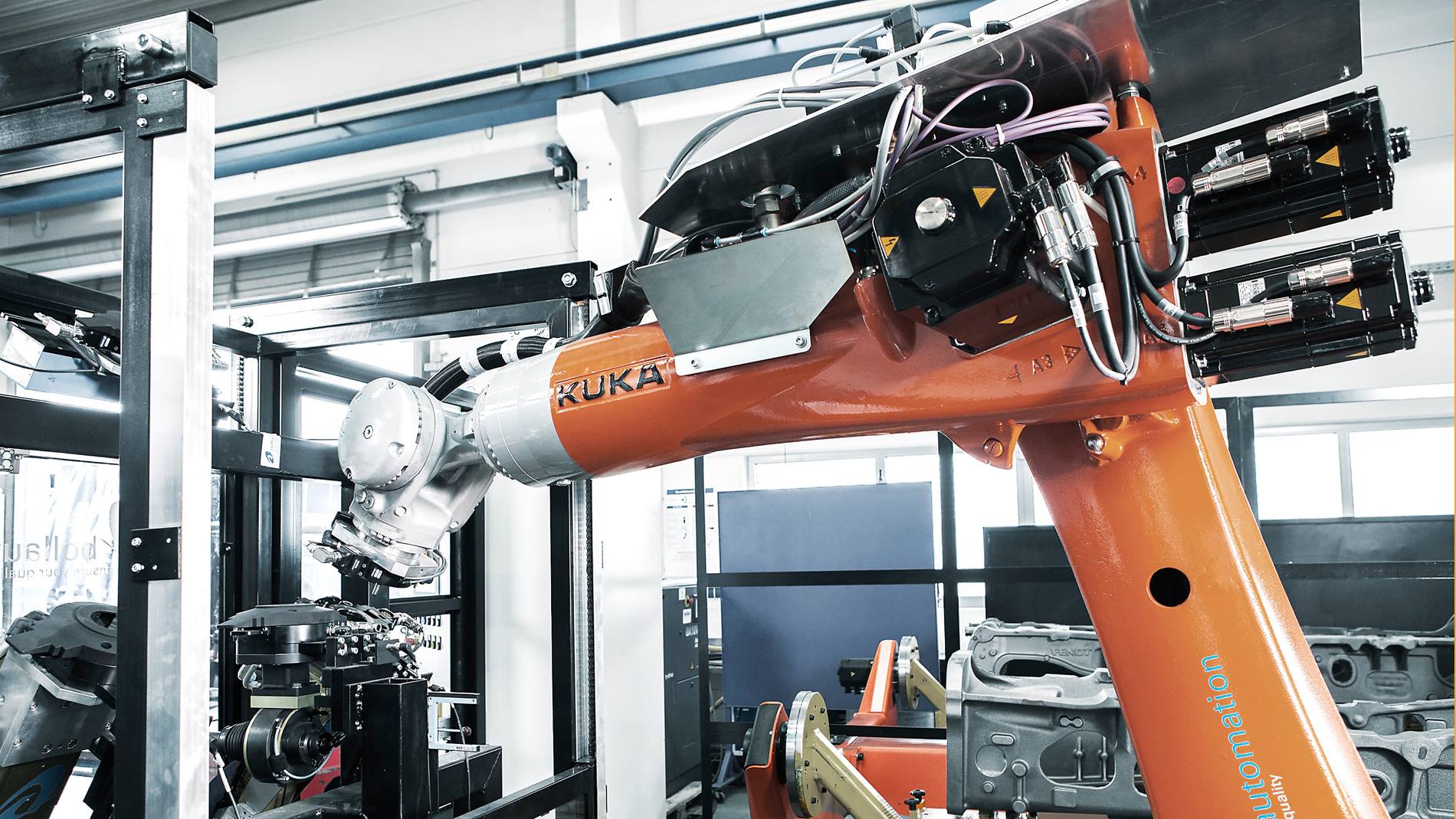
At Heidenreich & Harbeck, KUKA robots are using contour recognition to remove undefined casting burrs
Heidenreich & Harbeck have been manufacturing complex castings in Mölln since 1927
Finishing process despite undefined casting burr formations
Heidenreich & Harbeck – a company steeped in tradition – turned to Boll Automation to develop an automation solution which enables a fully automated, robot-based finishing process despite the undefined formation of casting burrs.

Foundry robots for operation in harsh environments
The robot used – the KUKA KR 120 R2900 F extra – was not only equipped with a tool changing system for picking up machining tools, but also with an additional sensor system that detects exact position of the various burr contours.
The six-axis robot is from the KUKA KR QUANTEC series for operation as a Foundry variant. KUKA KR QUANTEC robots are particularly compact and enable space-saving cell concepts. Beyond this, the 29 basic robot types of the series stand out for their range of payloads (from 90 to 300 kg), their reaches (from 2,500 to 3,900 mm) and their long intervals between maintenance (up to 20,000 hours of operation).
All models are installed on a compact base frame, with a nearly identical hole pattern for fastening to the mounting base. The foundry design also has a few additional advantages that were developed specifically for foundries: thanks to the use of special coatings, a heat-, corrosion-, alkali- and acid-resistant surface protects the robot. Additional protection is provided by special seals at the motor and gear unit flanges.
The foundry wrists hold gripper tooling made of special heat-resistant steel and are provided with a special aluminum white painting for even more heat resistance in this particularly critical area. For operation in harsh environments, it is also important that the electronic components in the robot are safely protected against dust and dirt throughout its service life. Atmospheric overpressure in the housing has proven successful here.
More humane work place conditions and optimal quality


