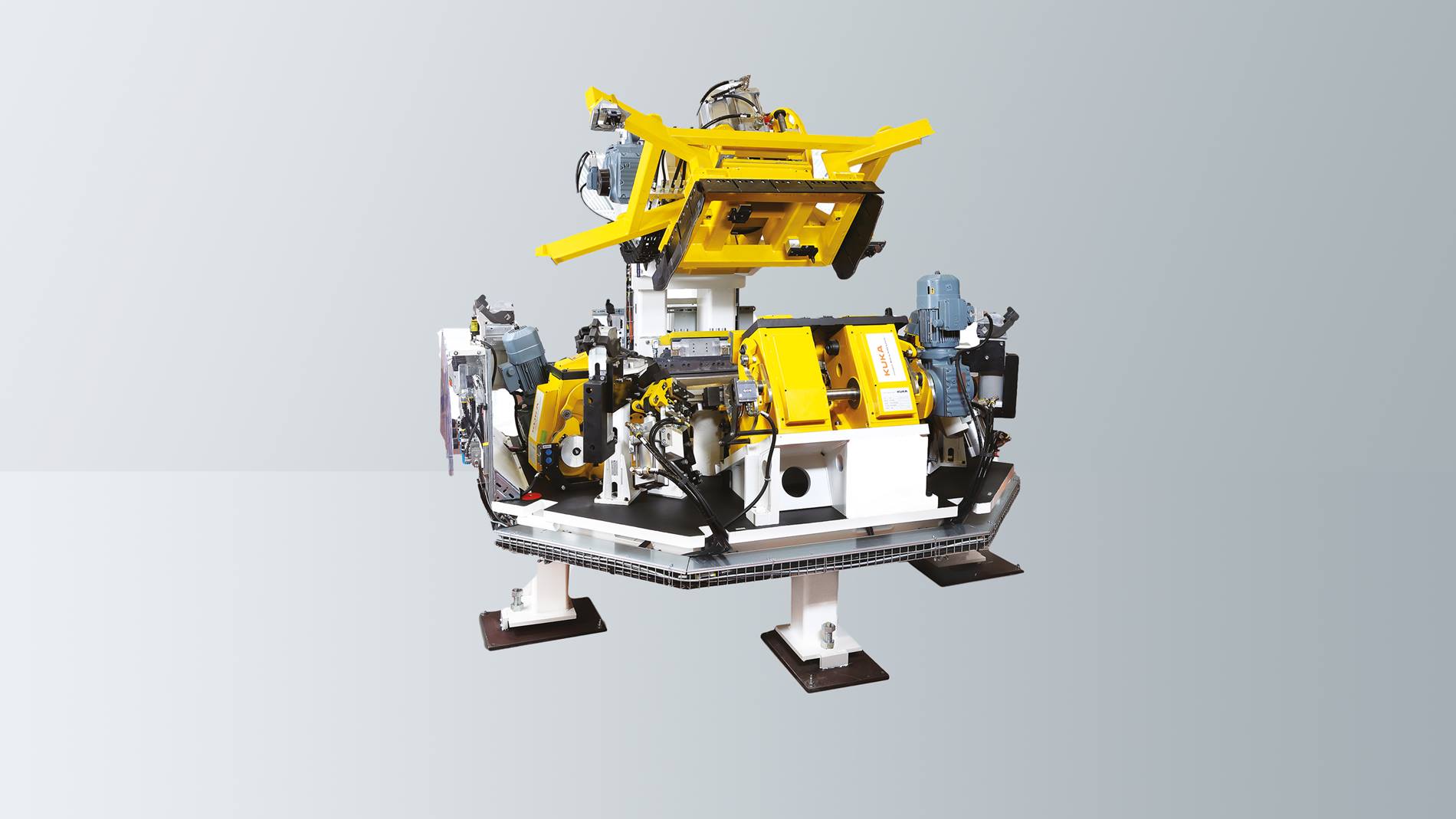
Hemming systems
KUKA has been installing product- and process-oriented hemming systems since 2001: depending on the cycle time requirements and workpiece size, we select either roller hemming or tabletop hemming or a mixed form comprising both processes. Our hemming solutions will enable you to produce more cost-effectively in the future.
Robotic roller hemming: a flexible 4.0 solution
Flexible production solutions have an important role to play in Industrie 4.0. In a volatile market situation dominated by ever broader product ranges and shorter life cycles, smart production is a decisive competitive factor. With our robotic roller hemming solutions it is possible to process different components and achieve optimal capacity utilization: additional tasks, such as welding or gripping, can be assigned to the robot.
- High Output Quality Hemming (HOQ): The HOQ hemming head enables controlled robotic hemming with hemming indicator.
- HOQ-S (Sunroof): The robot-guided hemming system on the sunroof enables you to achieve a short process time.
- HOQ-F (Flanging): The HOQ-F solution enables you to hem flange angles of greater than 105 degrees in a controlled manner. Additional pre-hemming stations are not required.
- Soft Touch Wheelarch Hemming (STW): We use STW Hemming in the automotive industry for the gentle hemming of wheelarches with a mobile understeel. In this way, multiple models can be manufactured in a single station.
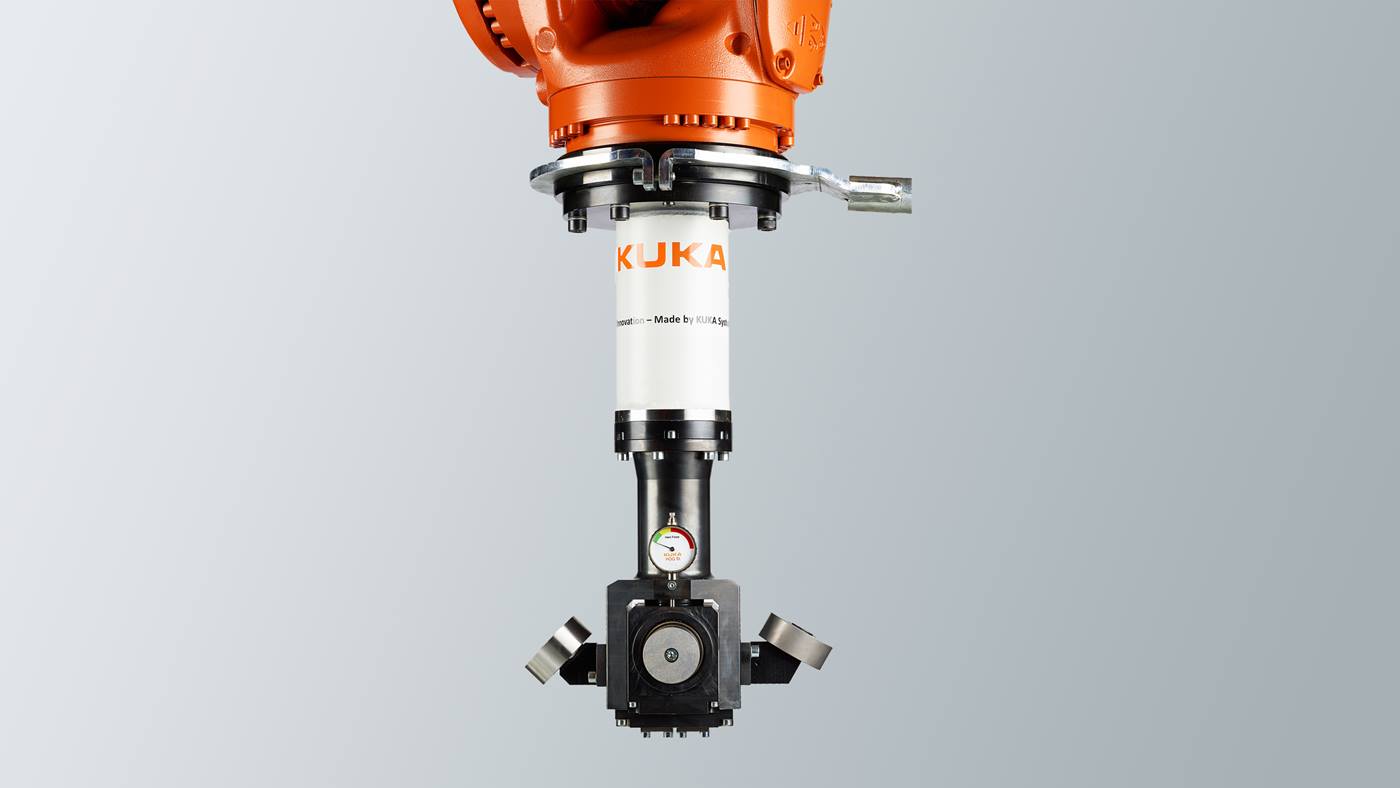
Tabletop hemming: large batch size with short cycle time
Tabletop hemming stands out due to its short process time. This hemming process is particularly suitable in the case of high-volume models with large batch sizes. Using standardized hemming modules, the machine can be adapted quickly and easily to the specific component geometry. In addition to the short cycle time, other advantages include:
- simple operation of the machine,
- modular configuration of the system and
- the possibility of performing both outer and inner hemming in a single machine.
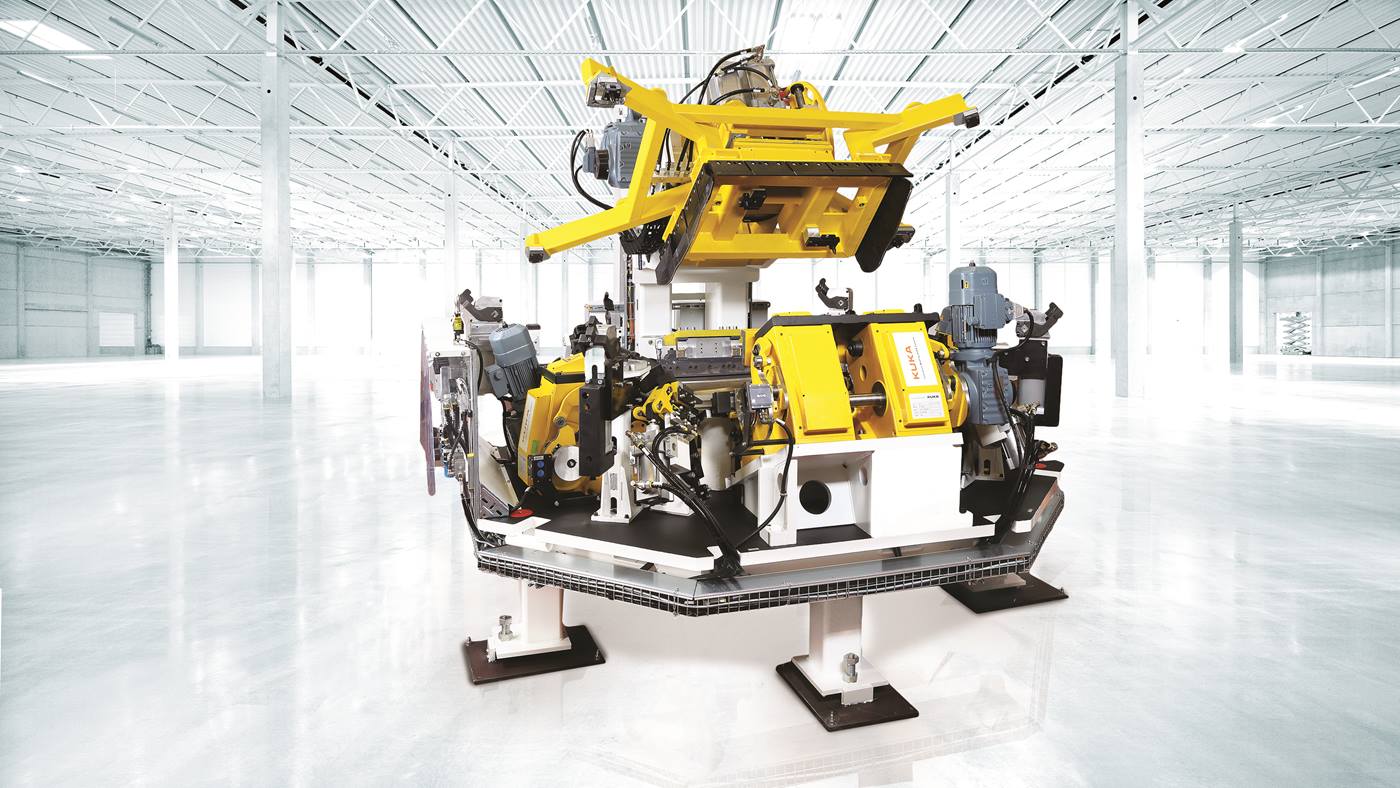
Give us a call and we will jointly determine the ideal hemming system for your production operations.