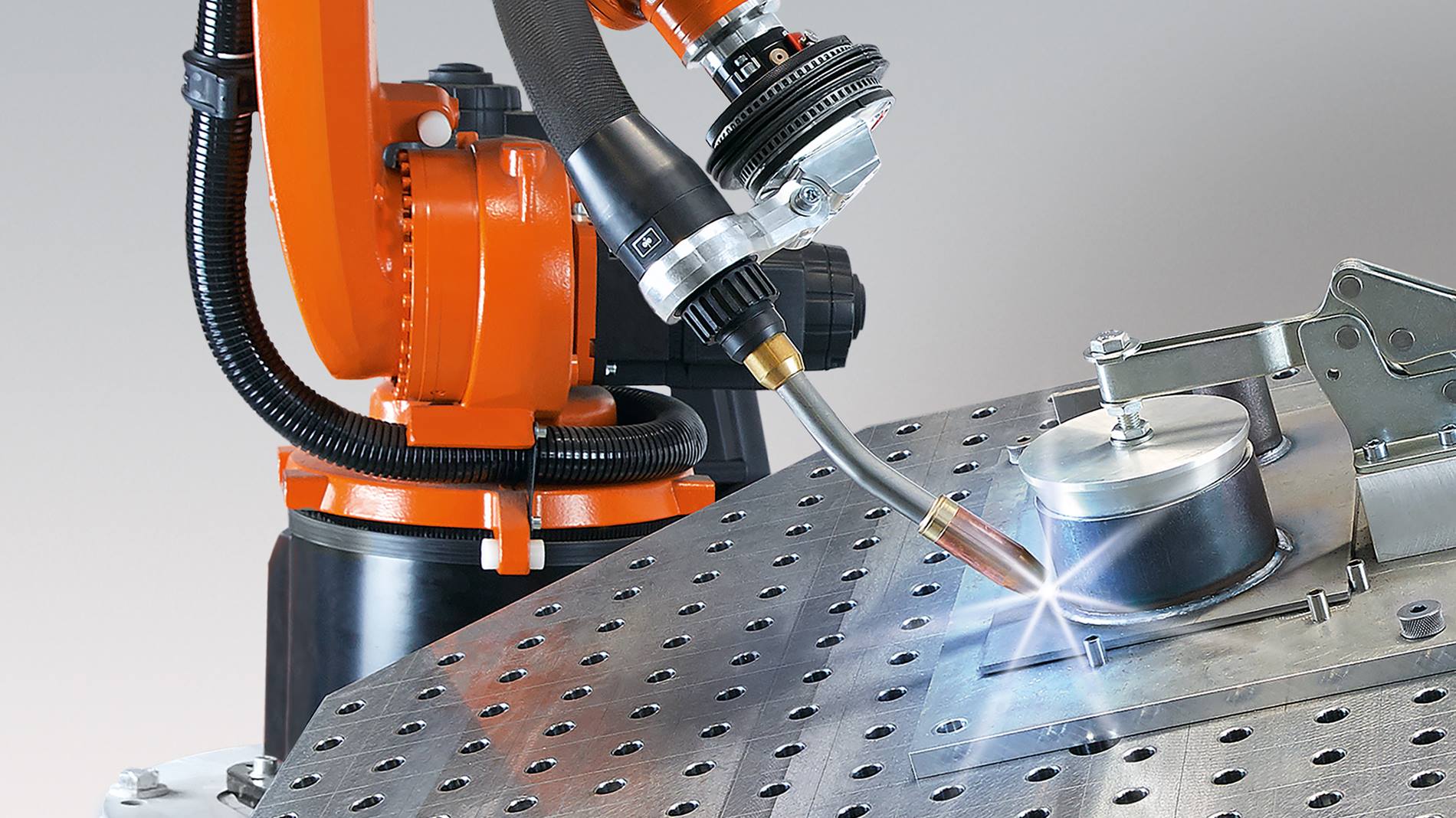
KUKA arc welding robots
Maximum productivity with lowest operating costs: KUKA welding robots ensure maximum efficiency and perfectly processed weld seams, even in continuous operation.
Maximum cost-effectiveness and flexibility: arc welding robots for all requirements
Find the welding specialist that is perfectly suited to your task:
Our robots are optimized for continuous operation with low operating and maintenance costs – ideal for tough welding conditions.
KR CYBERTECH nano ARC (6 – 8 kg payload capacity, hollow wrist)
The arc welding specialist is synonymous with utmost path accuracy – and comes as standard with the KUKA PathMode and absolutely accurate calibration. Three variants with reaches of 1,440 – 1,840 mm in conjunction with the hollow wrist enable optimal accessibility during welding.

KR CYBERTECH nano (6 – 10 kg payload capacity, standard wrist)
The KR CYBERTECH nano is equipped with a streamlined in-line wrist, enabling alternative mounting of a standard torch. It is thus also simple, for example, to mount triangulation sensors for seam tracking.

KR AGILUS (6 – 10 kg payload capacity)
The streamlined and compact KR AGILUS with reaches of 700-1,100 mm is ideal for confined spaces with small assemblies. It is particularly suitable for TIG welding and has a protection rating of IP67 as standard. Due to its low weight of approx. 55 kg, it can also be flexibly installed on simpler substructures. With the KR AGILUS and the compact KR C5 micro robot controller, even the smallest of compact cells are possible.

KR CYBERTECH (8 – 22 kg payload capacity)
With the streamlined in-line wrist and a payload capacity of up to 22 kg, the KR CYBERTECH comes into its own where heavy welding equipment or supplementary loads such as sensors are required.

KR CYBERTECH ARC (8 kg payload capacity)
The KR CYBERTECH ARC, with its hollow wrist, streamlined design and reach of 2,100 mm, is ideal for welding large metallic components.

KR IONTEC (20 – 70 kg payload capacity)
With its enormous reach of 3,100 mm and payload capacity of 20 to 70 kg, the KR IONTEC is suitable, for example, for welding large components or for welding applications with very heavy welding equipment such as laser optics, laser hybrid welding or laser powder deposition. Despite its size, the KR IONTEC also features outstanding path accuracy and a compact design.

More than just welding robots
In addition to dedicated arc welding applications, KUKA offers an extensive range of other robot models for a wide range of additional process tasks, e.g. loading/unloading with payload capacities of up to 1300 kg.
KUKA supports you before, during and after your production operations with a unique range of consulting and support services.
Efficient arc welding thanks to the right software
Welding software and sensor systems for maximum productivity and flexibility of your welding application
-
KUKA.ArcSense
Seam tracking with through-the-arc sensor (TAST): Available as an option for KUKA.ArcTech, KUKA.ArcSense analyzes the actual weld parameters and automatically compensates for tolerances such as heat distortion or workpiece inaccuracy. The through-the-arc sensor system ensures that the joint is made in the intended position. Combinable with all KUKA welding robots, KUKA.ArcSense is a software solution that ensures maximum quality and repeatability during the welding process. -
KUKA.ArcTech AdaptiveWelding
Automatic adaptation of the programmed weld parameters: Thanks to a configurable interface, weld parameters are adapted to workpiece tolerances and production-related irregularities between workpieces, e.g. the width of the weld joint. It is irrelevant here whether the deviations occur before or during welding. The continuous adaptation of the parameters ensures consistent and reliable weld seam quality and boosts the productivity of the application.
-
KUKA.ArcTech MultiLayer
Easy programming of multi-layer weld seams: With KUKA.ArcTech MultiLayer, you can quickly create a robot program for a multi-layer weld seam by simply programming the point coordinates of the root layer. Adaptation of the point coordinates of the multi-layer weld program is merely carried out in the root layer and the changes are automatically applied to the subsequent layers. Specifically for each filler and cover layer, the parameters for the offset values and the intended weld parameters can be stored in a database.
-
KUKA.SeamTech Finding
Workpiece and seam detection with intelligent line laser sensor: With a single measurement, the laser sensor captures multiple component geometry data which KUKA.SeamTech Finding uses to calculate a correction of the component, seam or individual path points quickly and precisely. Any deviations that occur can be compensated in up to 6 dimensions.
-
KUKA.SeamTech Tracking
Edge and seam tracking during welding: With an intelligent line laser sensor and a particularly high-performance EtherNet real-time interface, KUKA.SeamTech Tracking can perform an exact correction of the programmed welding path. Even at high weld velocities, the robot can independently adapt the seam position and length according to the specific component.
-
KUKA.TouchSense
Learn moreComponent and seam detection using the welding torch or an external sensor: KUKA.TouchSense compensates for deviations in the shape or position of workpieces by means of comparative measurements prior to welding. Any deviations that occur can be compensated in up to 6 dimensions. Combining this with the fast measurement inputs enables a higher search velocity and more precise measurement results. The component position can be determined by tactile or non-contact methods.
-
KUKA.Tracc TCP
Automatic tool center point (TCP) check: KUKA.Tracc TCP determines actual values of the TCP and ensures that the weld is carried out at the intended position. This automatically keeps the productivity of the welding cell at the highest level and thus prevents time-consuming manual reprogramming, e.g. after a collision or exchange of the torch neck due to wear. The special feature: during high-accuracy calibration of the TCP, KUKA.Tracc TCP determines the absolute value and therefore takes into account production-related tolerances of the welding torch.
-
KUKA.Sim
Offline programming of welding systems and welding robots: KUKA.Sim supports the simulation and creation of simple robot sequences. The extensive component library and Plug&Play functionality enable concept studies and reachability analyses without cycle time specifications. The real-time connection to KUKA.OfficeLite enables the analysis of cycle times, the creation of robot programs and the definition of kinematic systems. The simulations can be saved and played as a video or 3D PDF file at any time.
Download the KUKA welding robot brochure here
