
Using robots to promote electromobility and build safety valves for batteries
The boom in electromobility is also causing demand for batteries and the battery parts to skyrocket. Automotive supplier Hugo Benzing which is based in Korntal-Münchingen near Stuttgart and manufactures battery bursting discs, among other components, is feeling the effects of this. In the event of thermal overheating, the valves reduce the pressure in the battery, thus contributing significantly to the safety of electric cars. Valve production is challenging and highly synchronized – and therefore ideal for automation solutions.
Focus on safety in the production process

Two million valves per year



Robots move the individual parts through the cell
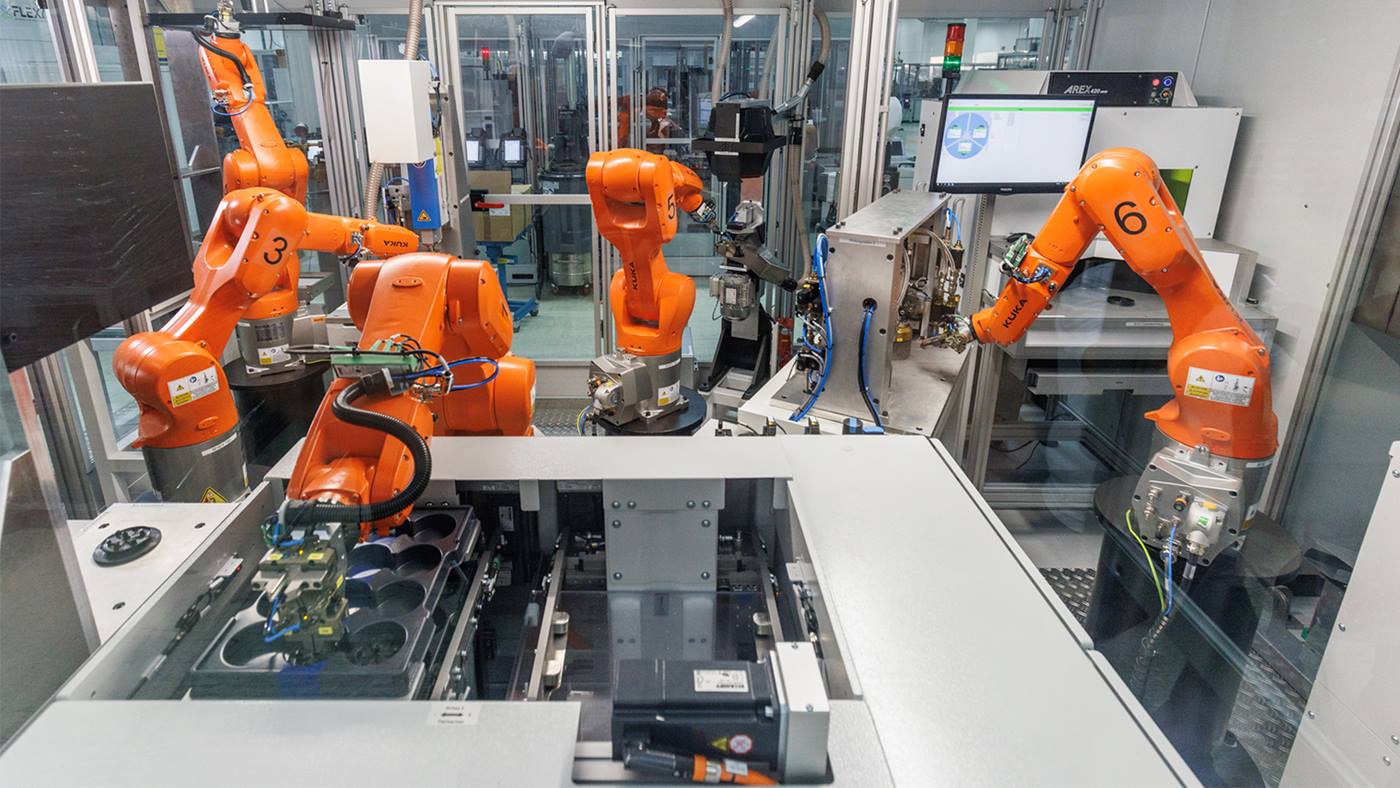
The machine operator can intervene at any time

Grippers demand maximum precision


To be the best supplier in this area, we need complete control of the process. We can only achieve this with automation.
More about the KUKA partner
