
Uso de robôs para promover a eletromobilidade e fabricar válvulas de segurança para baterias
O aumento da eletromobilidade também está causando um grande crescimento na demanda por baterias e seus componentes. O fornecedor de produtos para automóveis, Hugo Benzing, com sede em Korntal-Münchingen, perto de Stuttgart, e que fabrica discos de ruptura de baterias, entre outros componentes, está sentindo os efeitos disso. Em caso de superaquecimento térmico, as válvulas reduzem a pressão na bateria, o que contribui significativamente para a segurança dos carros elétricos. A produção de válvulas é desafiadora e altamente sincronizada - e, por isso, ideal para soluções de automação.
Foco na segurança no processo de produção

Dois milhões de válvulas por ano



Os robôs movimentam as peças individuais pela célula
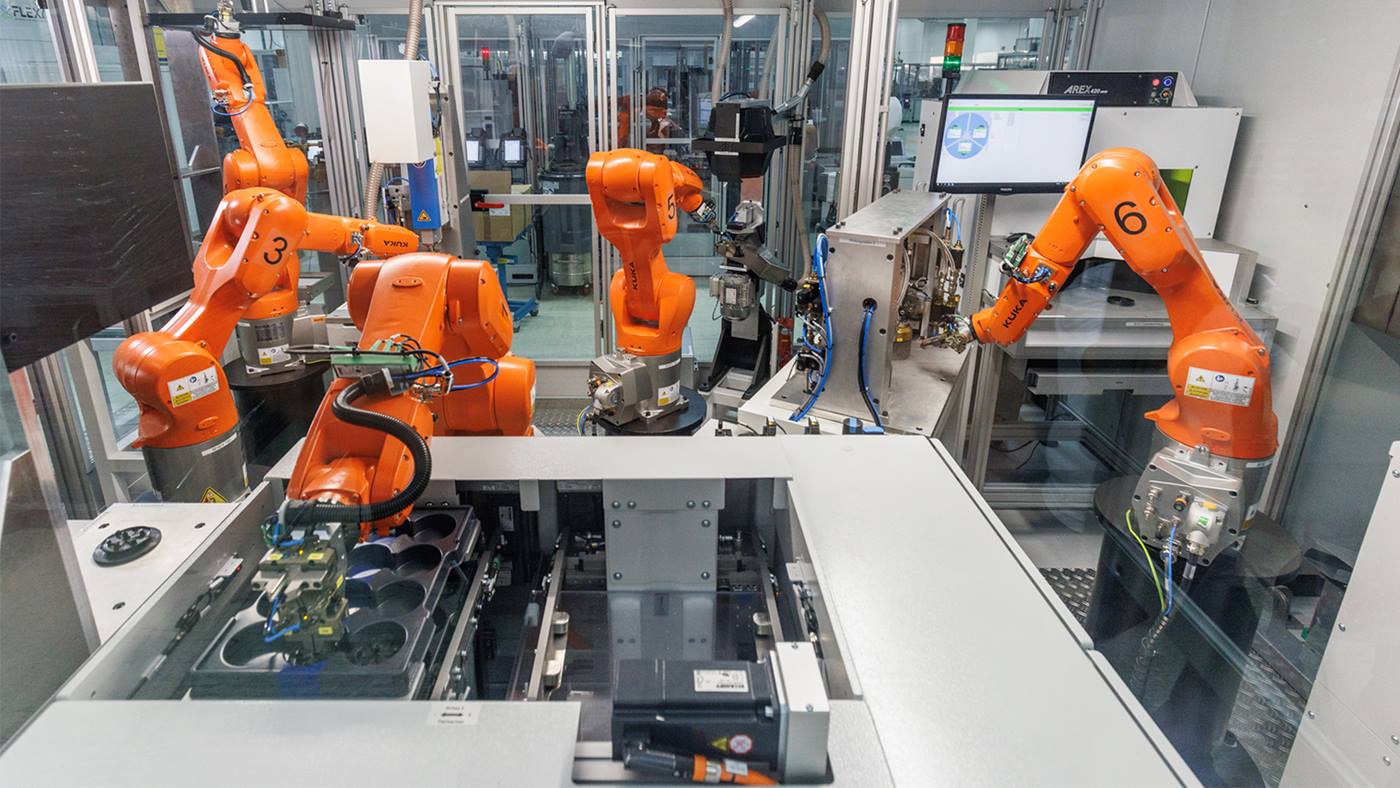
O operador da máquina pode intervir a qualquer momento

As garras requerem precisão máxima


Para sermos o melhor fornecedor nessa área, precisamos ter controle total sobre o processo. Isso somente pode ser alcançado com a automação.
Mais sobre o parceiro de KUKA
