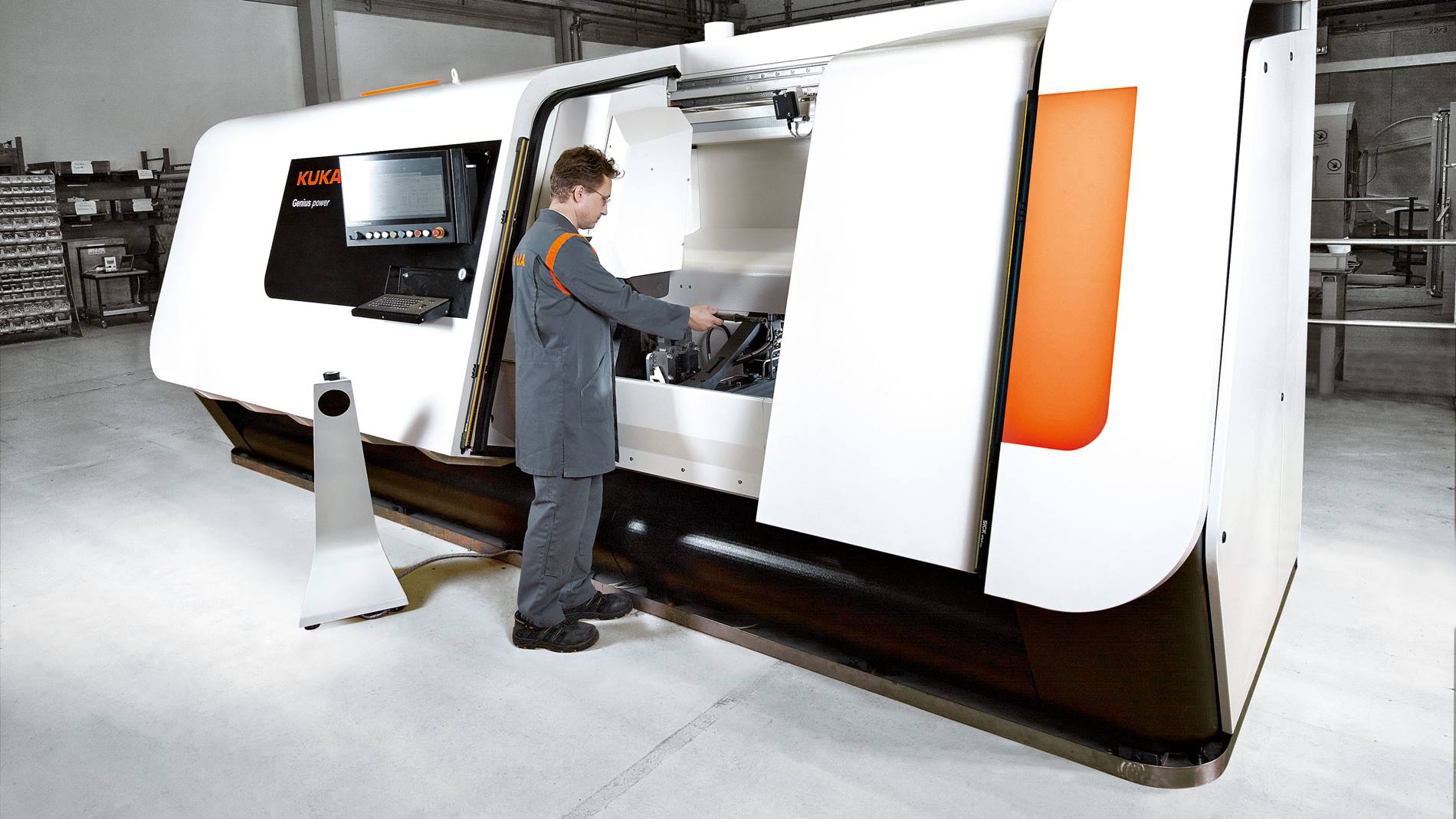
Rotary friction welding machines
KUKA and Thompson friction welding machines make the industrial joining of a broad range of materials simple and cost-effective. You can even weld challenging and safety-relevant material combinations with high quality in technology trends such as e-mobility and lightweight construction.
Standard and custom-tailored rotary friction welding machines with fixed headstock or moving headstock
Whether you opt for compact and universal series or special machines for particular components – we offer two different design types with fixed and moving headstocks that are tailored to your requirements as well as special sizes and designs on request.
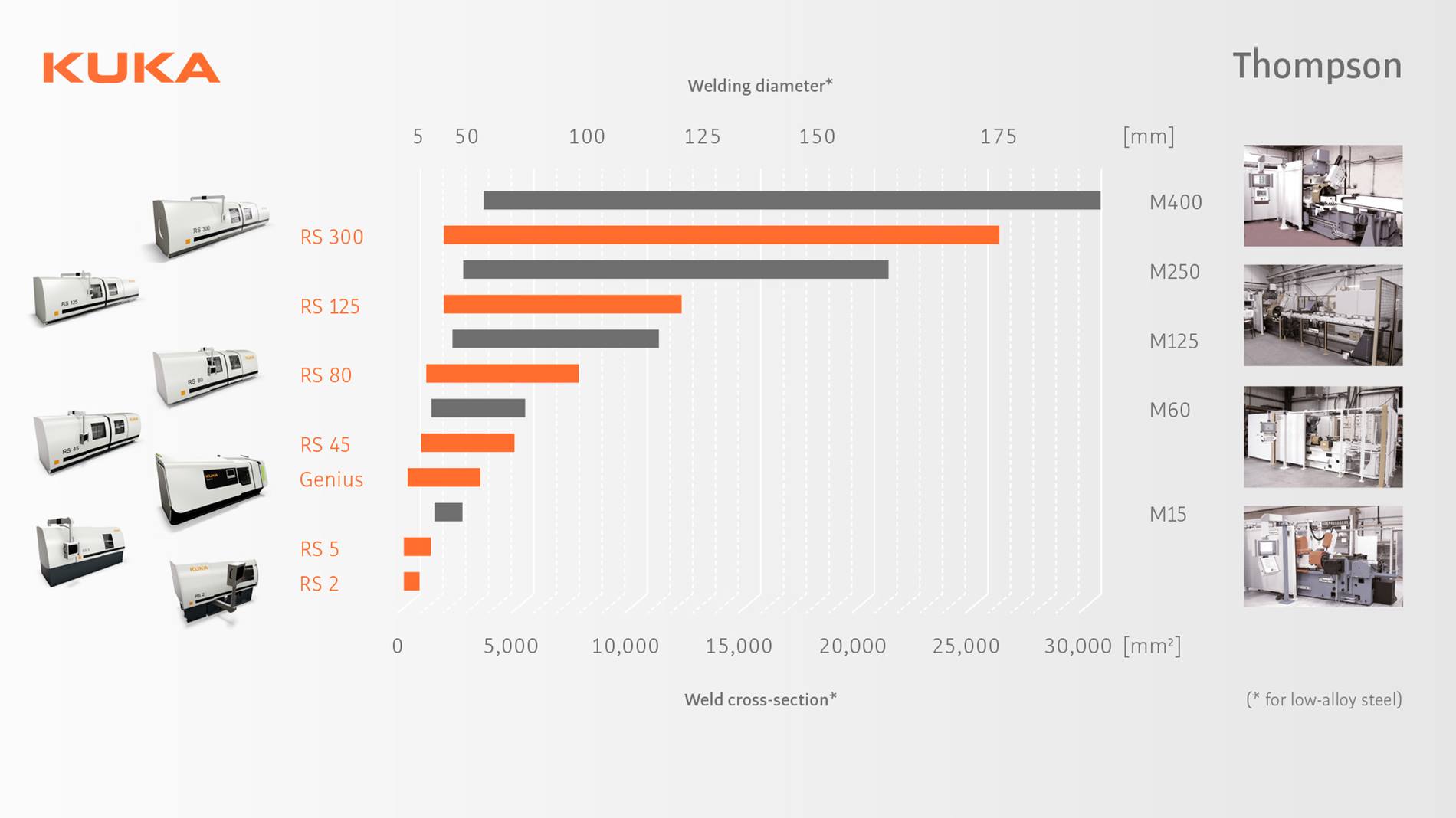
Rotary friction welding machines prepared for Industrie 4.0
Integrating rotary friction welding machines into your production network is a proven means of increasing your productivity. This requires open interfaces and intelligent control. As a manufacturer of flexible systems for automated production, we have the experience and expertise to develop and implement cost-effective complete solutions with high process reliability. With their easily accessible working area and the network capability of the controller, our rotary friction welding machines offer ideal conditions for the new era of Industrie 4.0.