KUKA Supplies System for Assembly of Battery Systems
The automotive industry is resolutely driving forward in the development of electromobility: Webasto, the automotive industry's global systems partner, is also entering the field of battery systems production. The production of battery packs for a European bus manufacturer has already started at the Webasto plant in Schierling in the Regensburg county, Bavaria. KUKA, the world's leading automation expert in the automotive industry, supplied the production system.
June 10, 2020
The automotive industry is undergoing the most significant change in its history. The model range of electric and hybrid vehicles is expanding dramatically. The automotive industry's electromobility offensive is also impacting on production processes: Because conventional production lines for automobiles cannot be transferred to the manufacture of electrified powertrains.

As an automation specialist in the automotive industry, we are already working on standardized manufacturing and assembly solutions for efficient battery pack and battery module production. KUKA also supplies production and assembly lines for fuel cells or their components.
Webasto started production of its standard batteries at the beginning of 2020. A finished battery pack is produced approximately every 15 minutes. The system is designed as a multi-product line and enables the production of different battery types.
2016: Webasto extends portfolio with charging solutions and battery systems
"We are opening a new chapter with battery production.", says Dr. Hartung Wilstermann, globally responsible for the battery business at Webasto. In 2016, the decision was made to expand the product portfolio: in addition to the core business with roof and thermal systems, the automotive supplier now also produces charging solutions and battery systems for electrified vehicles of all kinds. "As a long-standing partner of the automotive industry, we have been shaping trends and developments in the industry together with our customers.", says Wilstermann. "In addition, as the world market leader in our existing business, we have competencies that play an important role, especially for solutions in electromobility. These include comprehensive know-how in thermal management, the integration of large components in vehicles and many years of experience in industrialization."

Assembly and handling of a battery requires highest precision
The battery is the heart of electric vehicles. It consists of many individual components and electronic parts. Assembly and handling therefore require high precision in a limited space. "We have risen to the challenge and efficiently combined all the necessary process steps.", says Dr. Döhner from KUKA. Driverless transport vehicles (abbreviated FTF or AGVs) are used to transport the required battery components to the individual production stations. The AGV also serves as a kind of central supermarket, supplying side-mounted drawers containing, for example, templates as safety instruments and positioning aids for the manual processing steps of the workers. "Our aim was to simplify the work processes in battery pack production and to safeguard them in such a way that the workers' safety equipment can be reduced as far as possible.", says Dr. Döhner from KUKA.
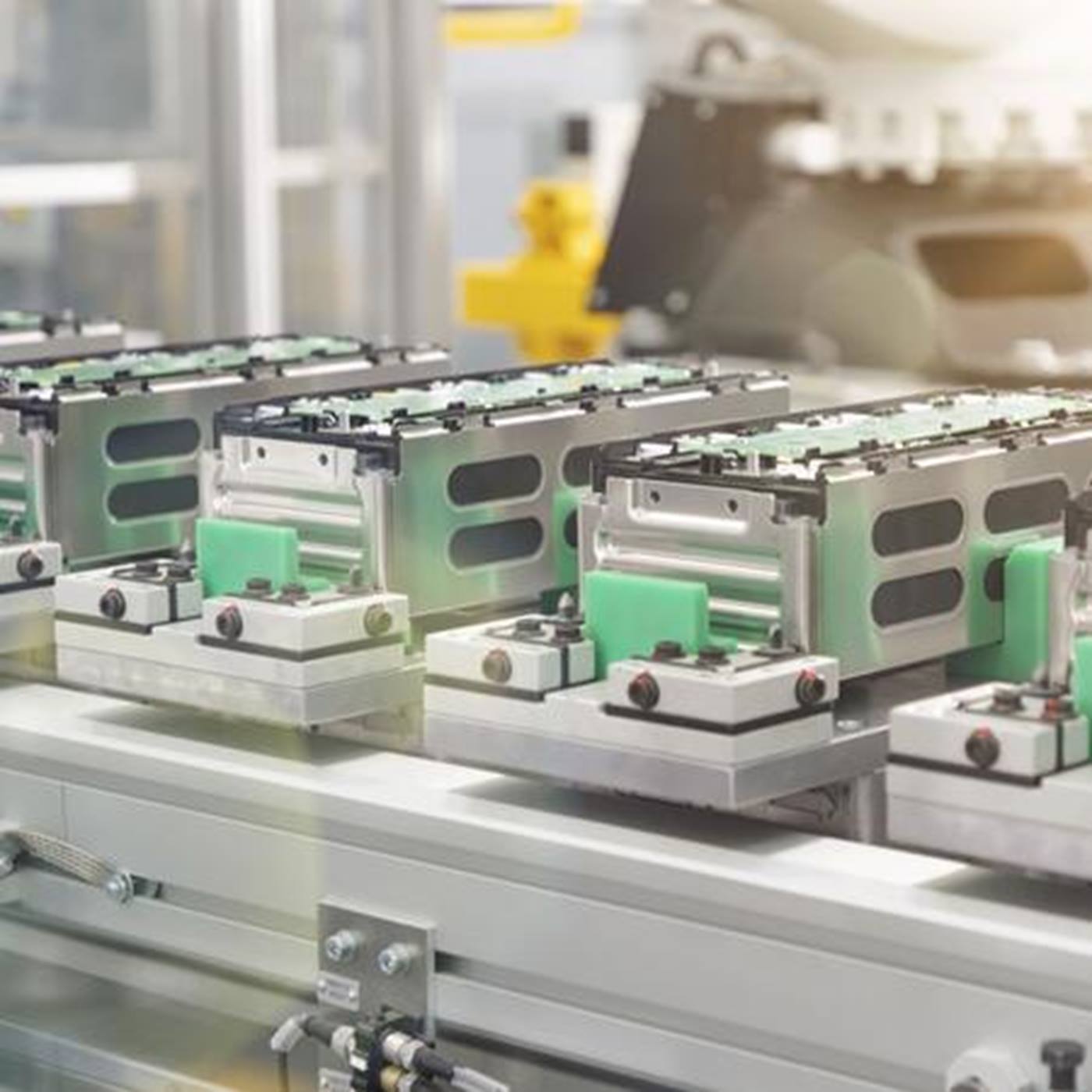