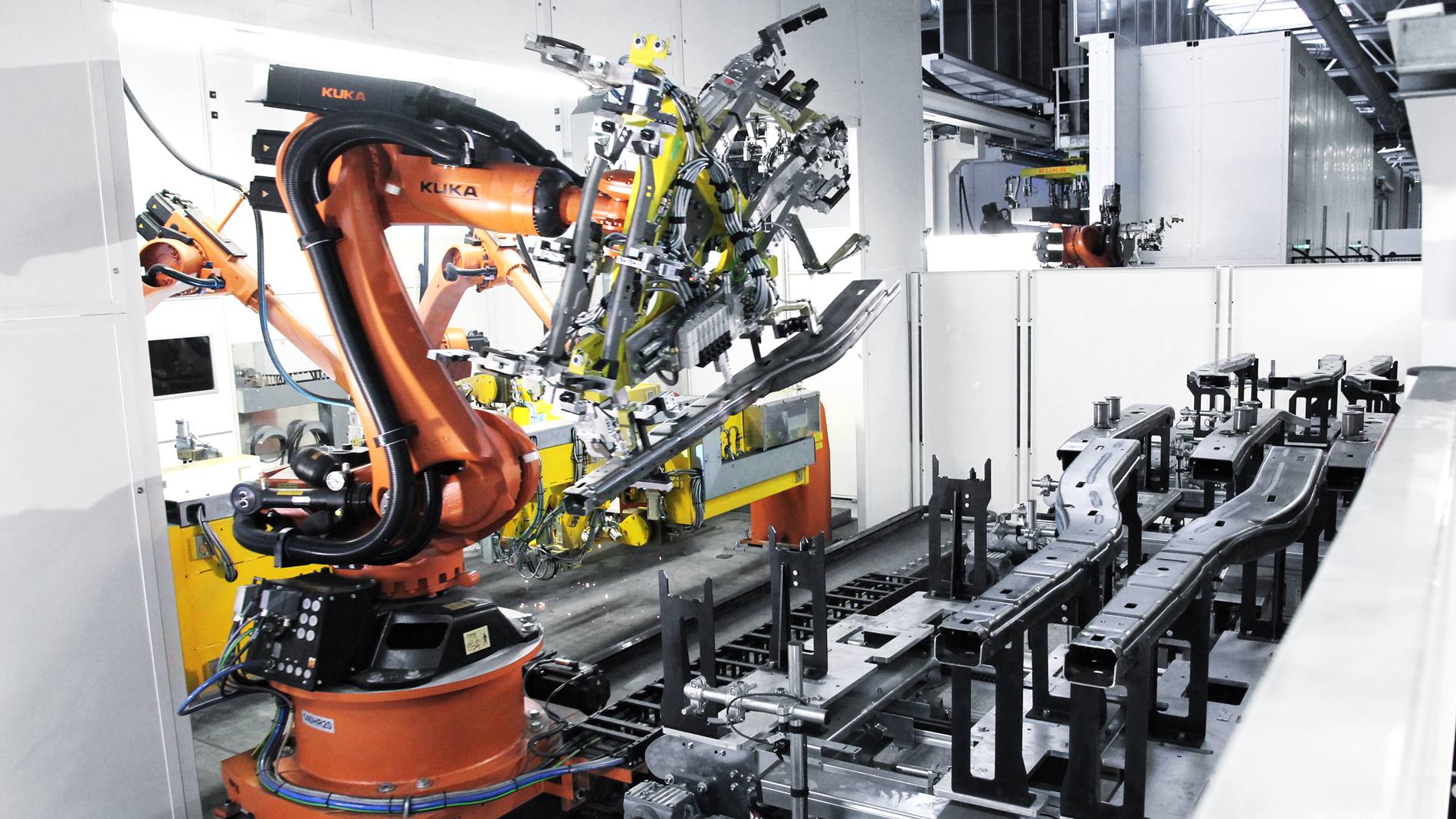
Fully automatic arc welding line from KUKA Systems at Gestamp
The metal-forming and chassis specialists at Gestamp manufacture ladder frames for the VW plant in Hanover. The Gestamp plant in Bielefeld is now using a fully automatic arc welding system from KUKA Systems to ensure the highest quality, proven process reliability and high output with minimal manpower requirements.
The task
The finished Amarok ladder frame weighs 230 kilograms, is almost five meters long and nearly one and a half meters wide, making it the largest part ever produced at the Gestamp plant in Bielefeld. Well over 200 individual steel parts are used to produce it.
The very tight deadlines and space restrictions presented a special challenge during the planning stage. Every last bit of the 3,000 square meters had to be used efficiently for production and logistics.

The solution
The subassemblies of the ladder frame (side members, cross members and add-on parts) are manufactured in 14 highly standardized welding stations, each with one component loading station and two fixtures. KUKA dual turnover positioners are used to place all components in the best position with regard to ergonomics or processes. This way, operators or robots have optimal access to the components at all times. The finished side members and cross members are then picked up by fully automated linear gantries.

The experts at KUKA combined professional project management with creative solutions – the perfect choice for us. All of the agreed measures were implemented promptly and systematically.

