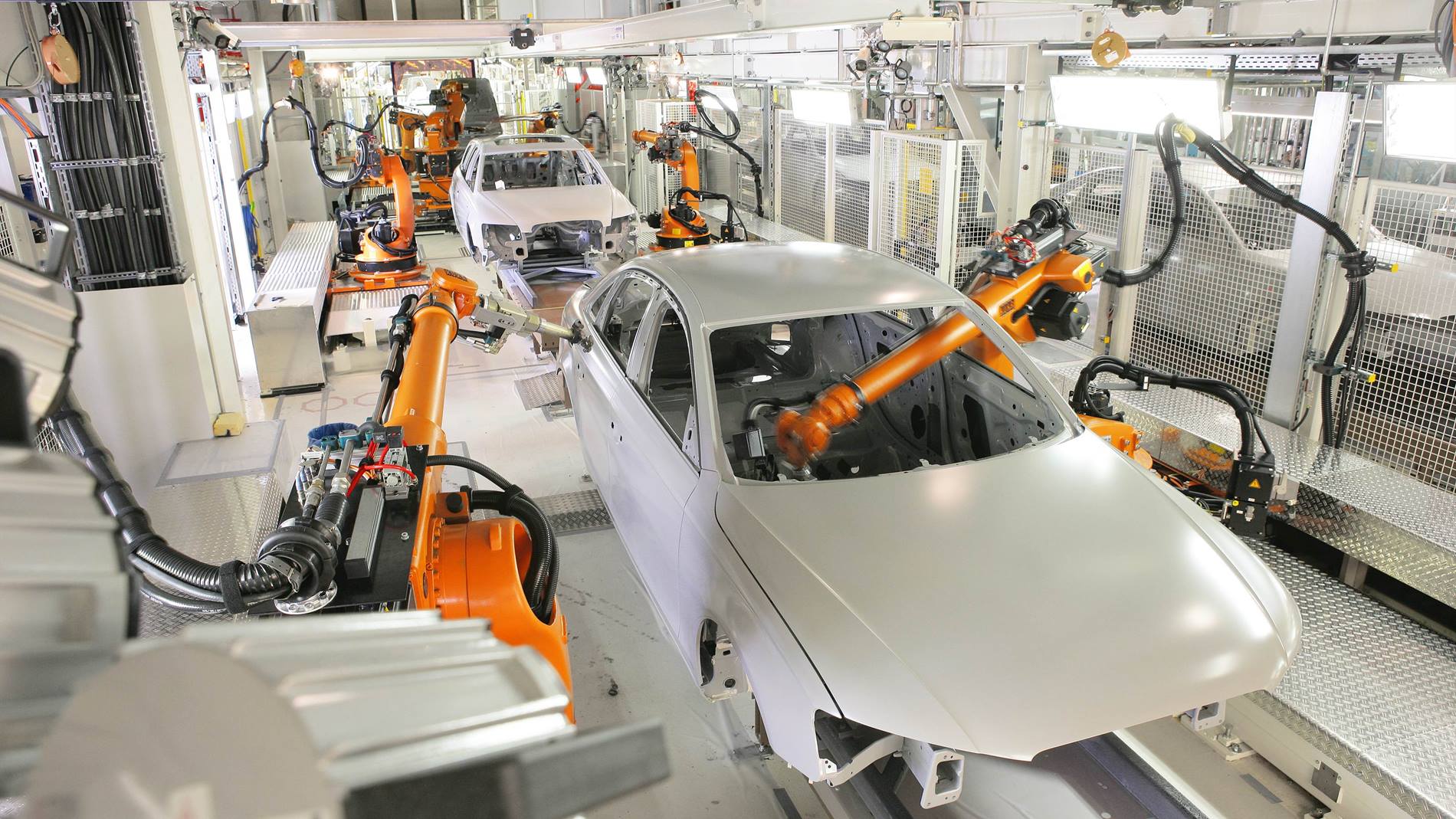
Paint shop: more than good looks
The process sequence of a car in a paint shop is multifaceted: from seam sealing and cavity corrosion prevention to wax cleaning. Many process steps are required to ensure that the vehicle body has sufficient corrosion protection – as well as a brilliant glossy finish.
The appearance of the vehicle is defined in the paint shop. This is where the color and the required shine are provided. In addition to esthetic aspects, the individual surface treatments also perform important functional tasks, such as corrosion protection, soundproofing and vibration damping.
KUKA covers the following automation steps in the paint shop: various cleaning and bonding operations, seam sealing, quality inspections with the LBR iiwa lightweight robot and acoustic/vibration damping with sprayable damping material (SDM).
Acoustic damping with SDM
Automate your production with the flexible KUKA SDM system concept for the acoustic damping of vehicle bodies. You receive the following basic components that can be custom-adapted or expanded as required:
- KUKA KR 30 L16 industrial robot: these robots apply the damping material and open doors and hatches.
- KUKA linear units enlarge the workspace of industrial robots and thus enable the processing of different vehicle models.
- KUKA system technology: application systems with various different nozzles that apply the material, and the corresponding measurement, control and conveyor systems from KUKA ensure smooth operation.
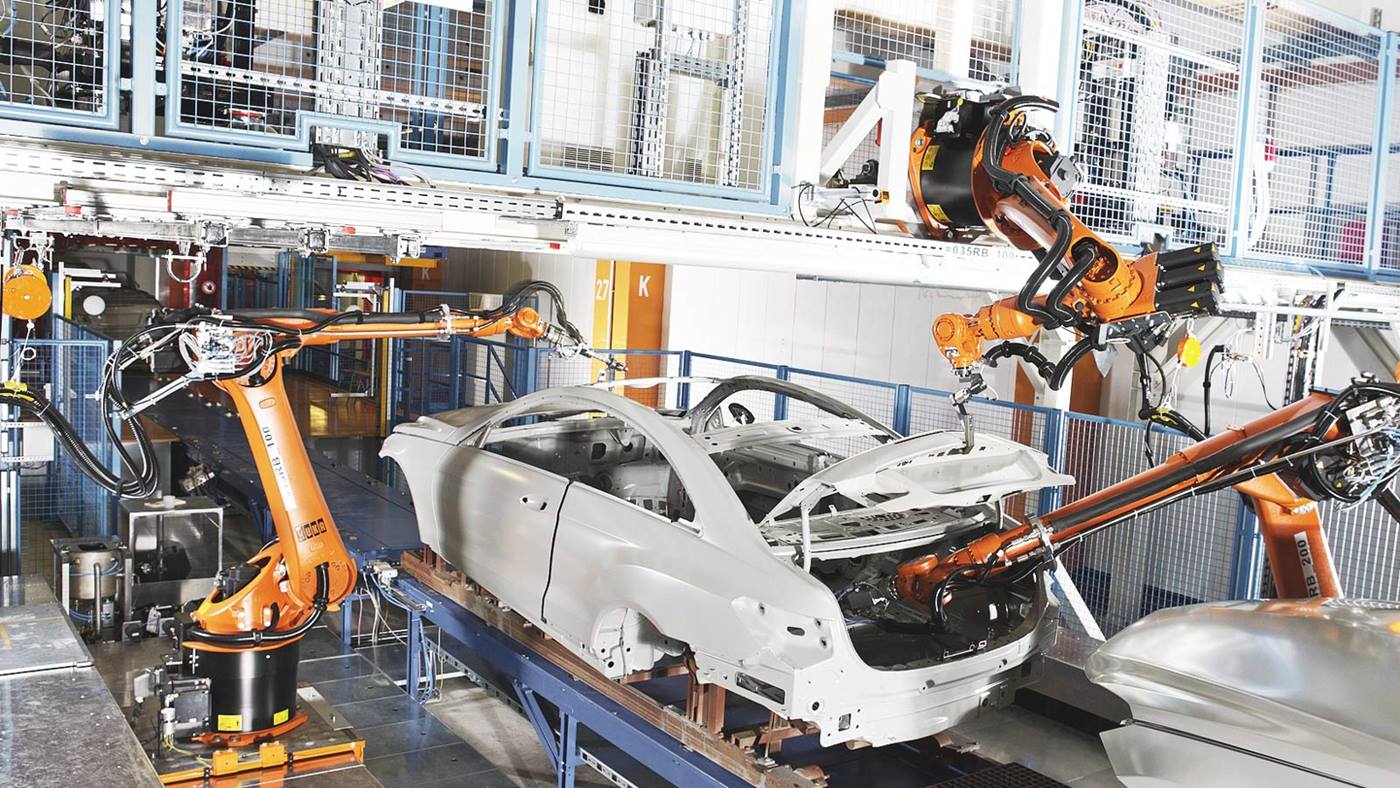
LBR iiwa: painting and sealing seams
The painting and sealing of seams inside vehicles is an ergonomically inconvenient and arduous routine operation. The LBR iiwa robotic colleague can relieve the human operator. The sensitive assistant can reach its place of work by means of swivel units or linear axes.
Moreover, the lightweight robot can also perform the following tasks:
- Cleaning: It uses compressed air, for example, to clean the vehicle body after cathodic dip painting (CDP) or removes drops of wax with a special tool.
- Quality inspection: Seams that have previously been applied automatically can then be inspected by the LBR iiwa and rectified if necessary.
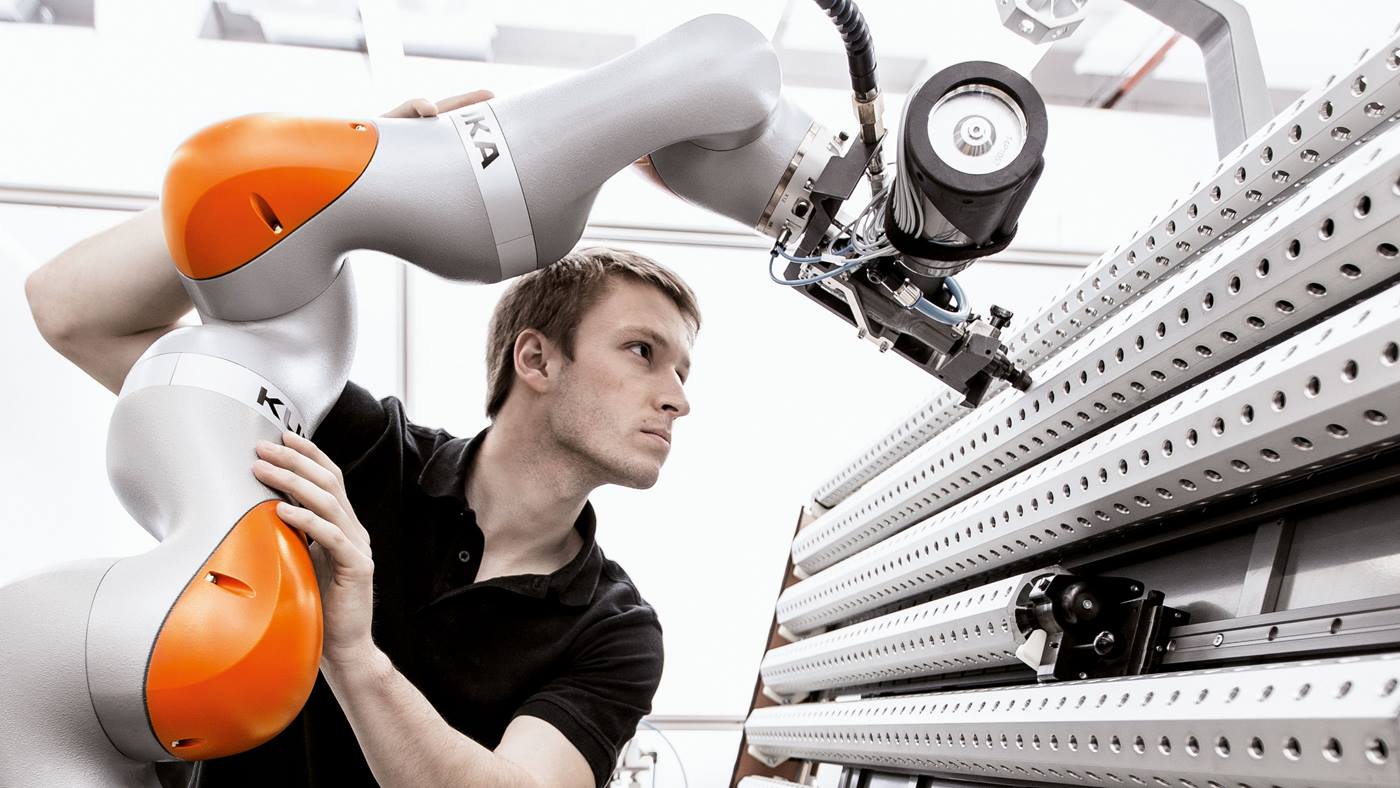
Cavity corrosion prevention of vehicle bodies
Temperature fluctuations, dirt from the road and salt crystals: over time, various environmental influences result in damage to the vehicle body due to corrosion. To protect the rocker panels, beams and frame against this, a cavity protection wax is applied at the corresponding points.
For this, KUKA uses both punctual and sequential wax application processes to make your production even more cost-effective. The wax is applied using spray nozzles whose shape and spray pattern are adapted to the cavities.
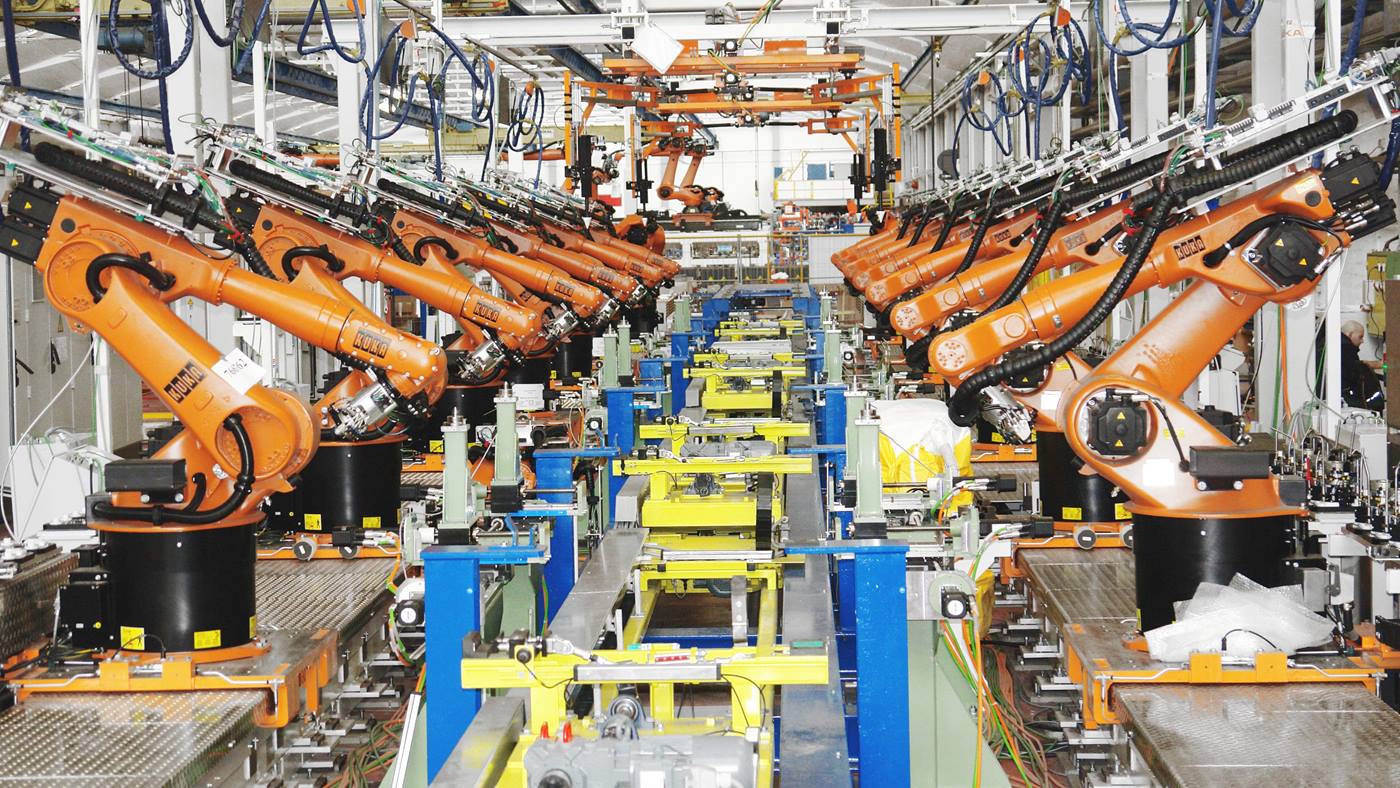